DETAIL Award 2022
Kiln Tower in Cham
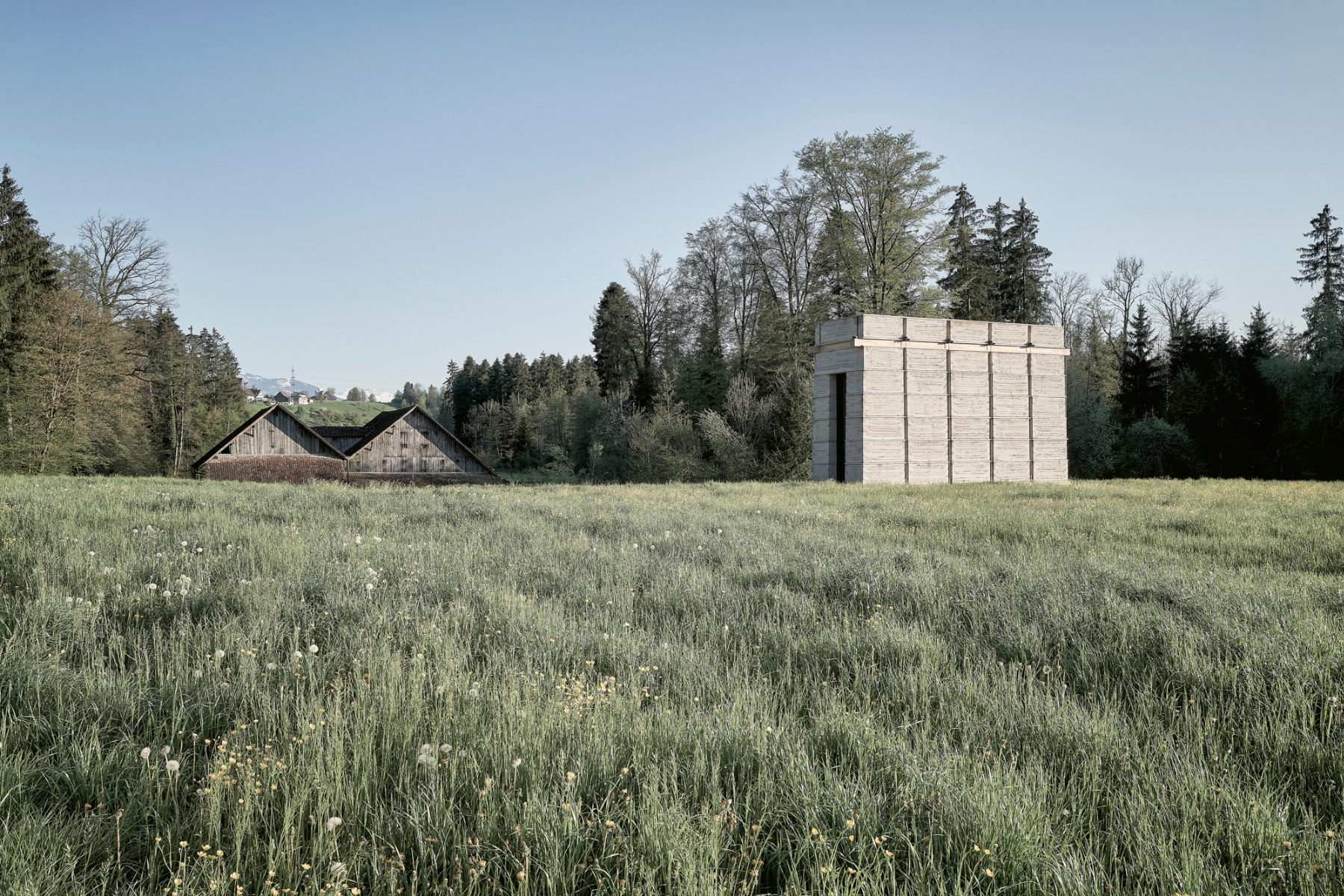
© Kuster Frey, Zurich
Lorem Ipsum: Zwischenüberschrift
Boltshauser Architects won the Detail Award 2022 with their kiln tower for the Brickworks Museum in Cham. The unconventional tower complements the existing Brickworks Museum ensemble. An experiment and exhibit in one, it is made of a material that appeals to all the senses – clay. Visitors approaching the building might be reminded of the tower tombs in Oman or the nuraghi of Sardinia. Measuring about 10 m high, 13 m deep, and 4 m wide, the earthen tower tapers slightly towards the top. With its black steel entrance portal, it resembles a place of worship with transcendental significance.
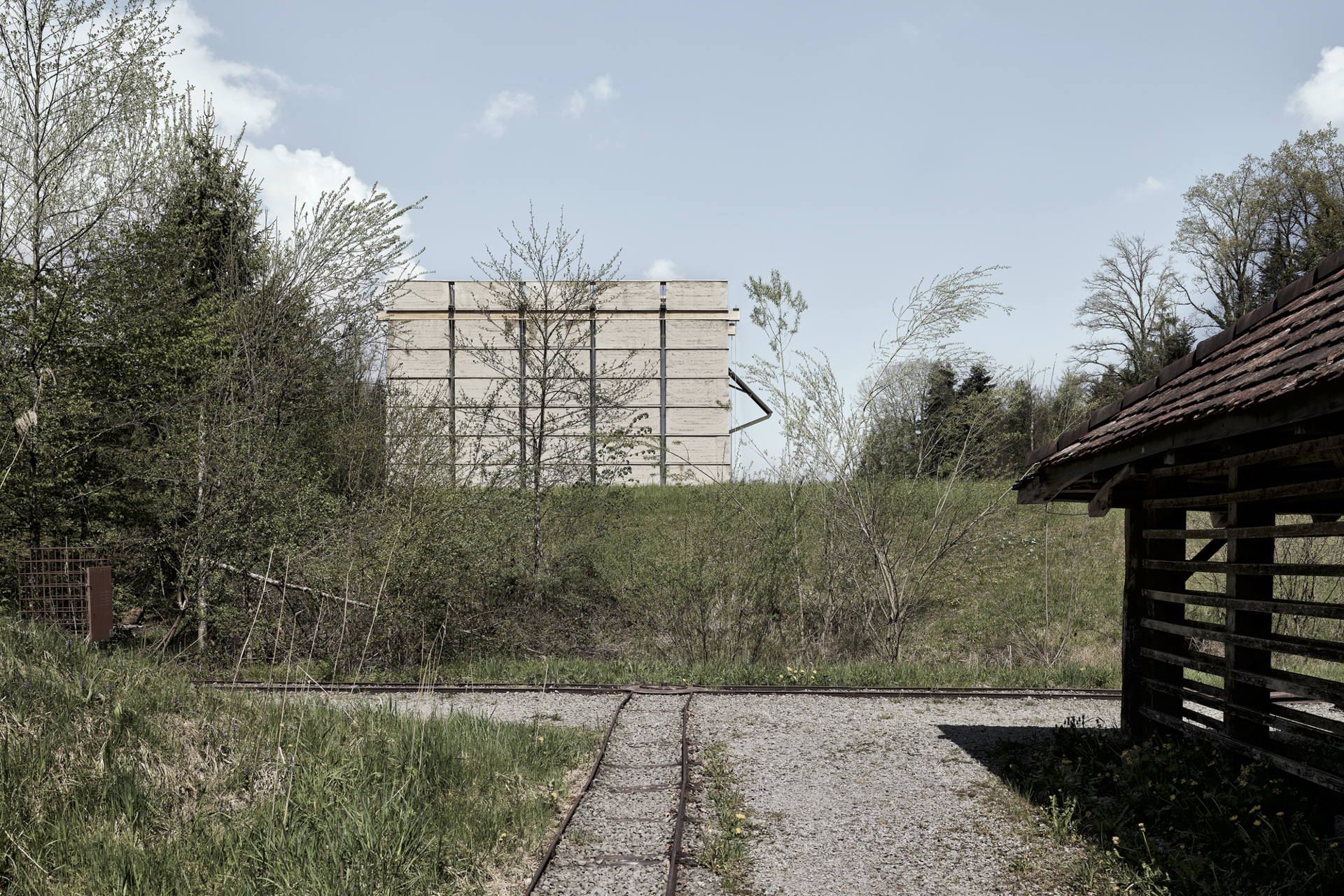
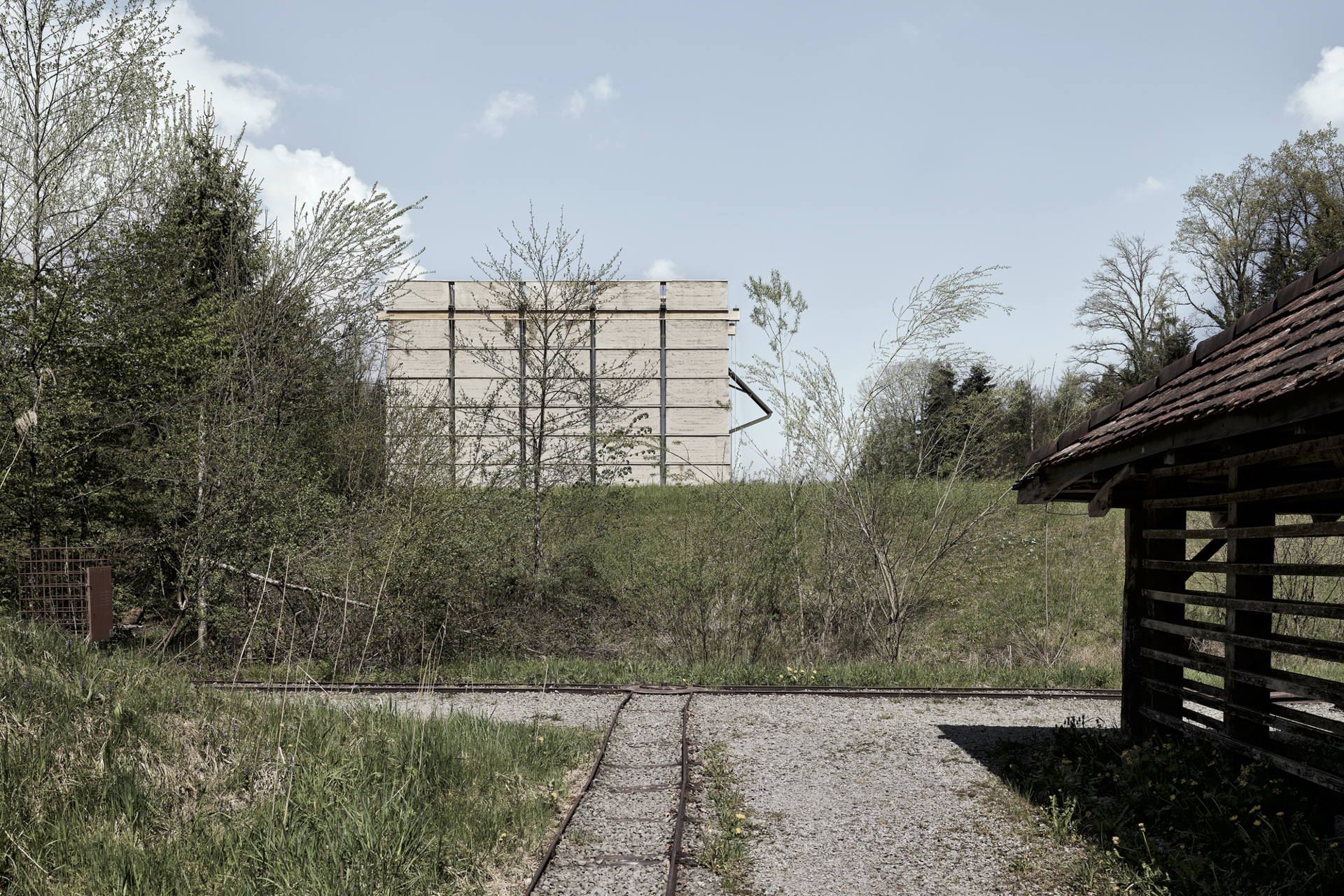
© Kuster Frey, Zurich
Lorem Ipsum: Zwischenüberschrift
Arriving in front of the massive block, its function as a lookout tower finally becomes apparent. At 8 m above the ground, the visitors’ platform provides a good view of the surrounding area as well as the historic clay pit of the last-remaining handmade brickworks in German-speaking Switzerland.
Building with clay has a long tradition but receded in popularity as other building materials, such as concrete and plastics, were further developed with industrialization. For some time now, however, building with clay has received growing attention as a viable low-carbon construction method, reinforced by the need to build sustainably. Earthen constructions consume only 10 % of the energy compared to concrete or brick.
Lorem Ipsum: Zwischenüberschrift
What makes the tower in the Brickworks Museum so unique is its construction method using rammed earth. Though it may seem antiquated, building with clay is booming. In 2017, students at the Technical University of Munich worked on the design of the new kiln tower on the site with visiting professor Roger Boltshauser. The project was continued under expert guidance at an ETH Zurich summer school programme with around 30 students from ETH Zurich, TU Munich, and other universities in Switzerland and abroad, proving itself as a compelling self-build project.
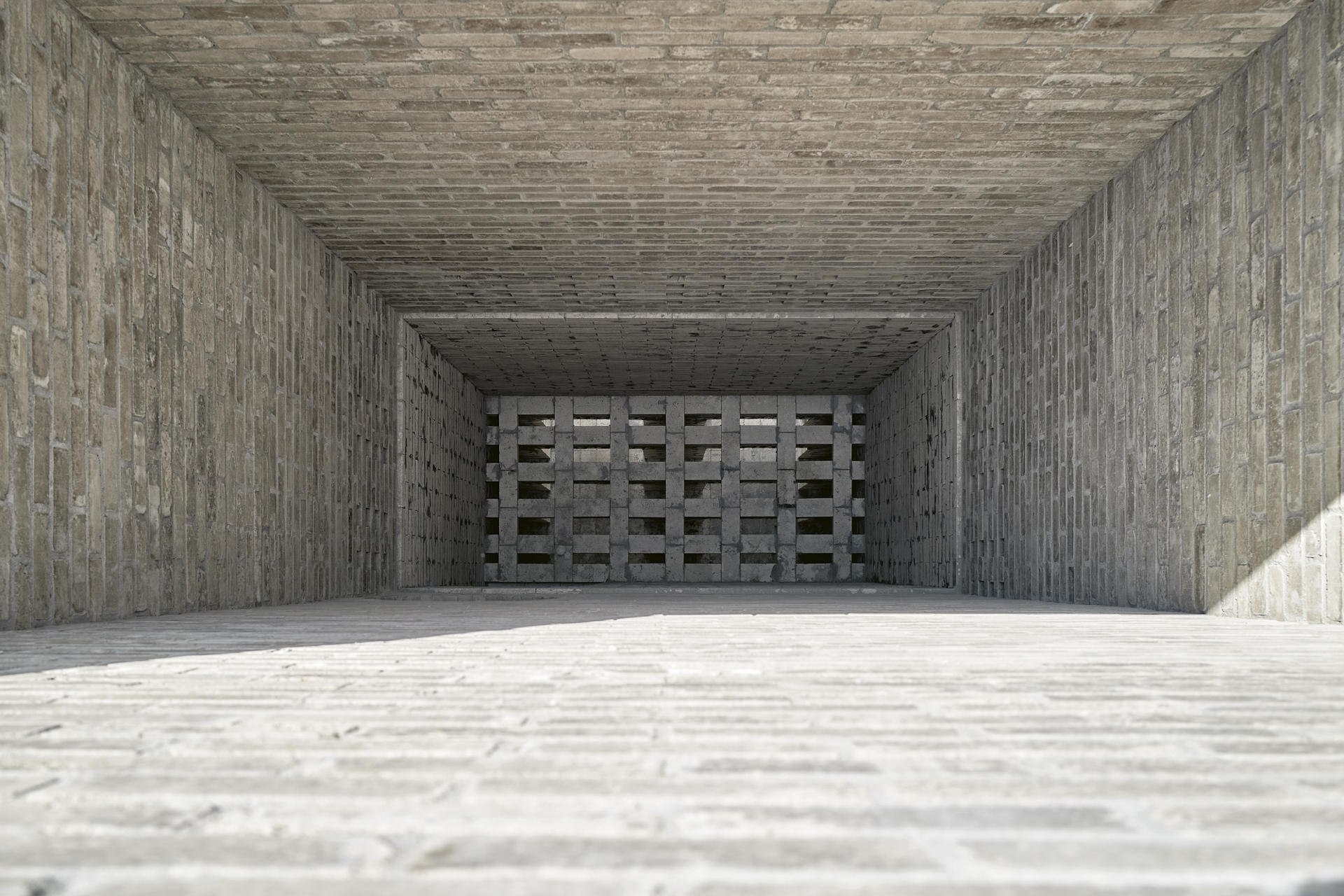
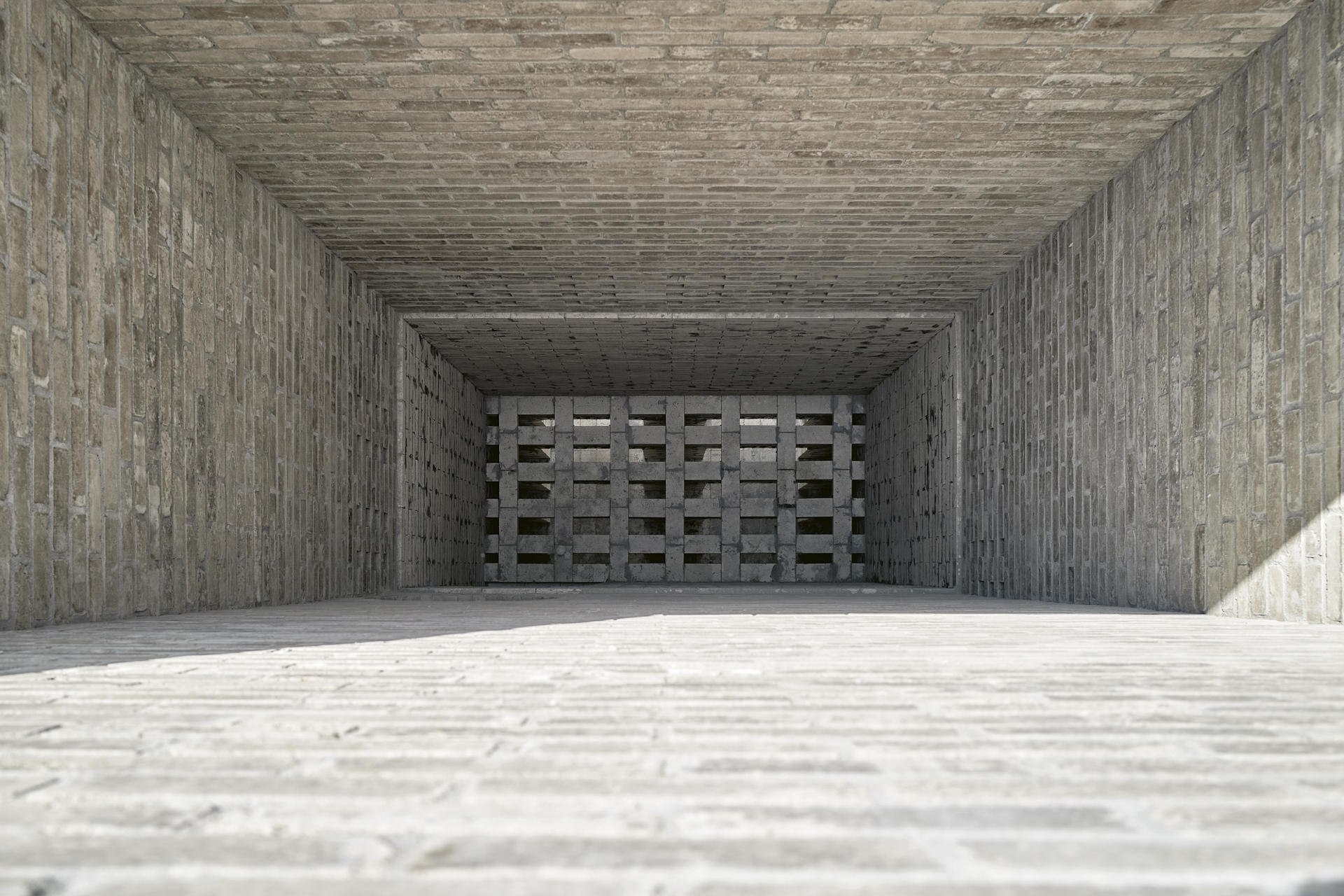
© Kuster Frey, Zurich
Lorem Ipsum: Zwischenüberschrift
They used a fat clay mixed with demolition rubble, as preparing the loam on-site would have been too time-consuming. A highlight of the project is how the earthen modules are stacked. Each element rests on the wooden plate on which it was compressed, which also facilitated the transport of the still soft rammed-earth blocks. One of the structure’s significant innovations was the integration of those base plates into the wall structure. Two grooves on the underside of each plate served as guides for tension cables. A weatherboard was mounted on each plate, which protects the earth from washing away and highlights the joining principle. Horizontal supports and corners made of trass lime mortar were pressed into the blocks as additional erosion protection.
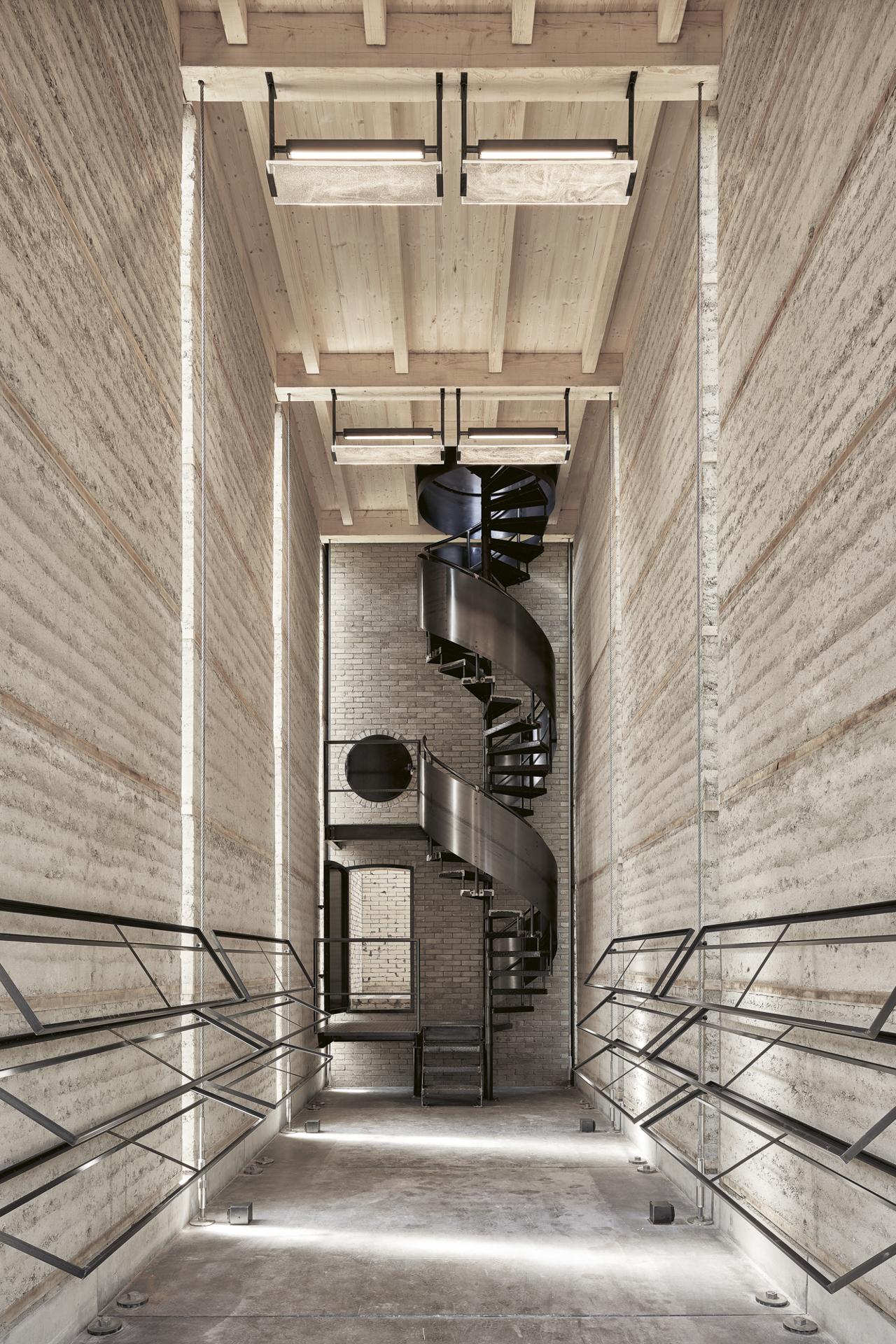
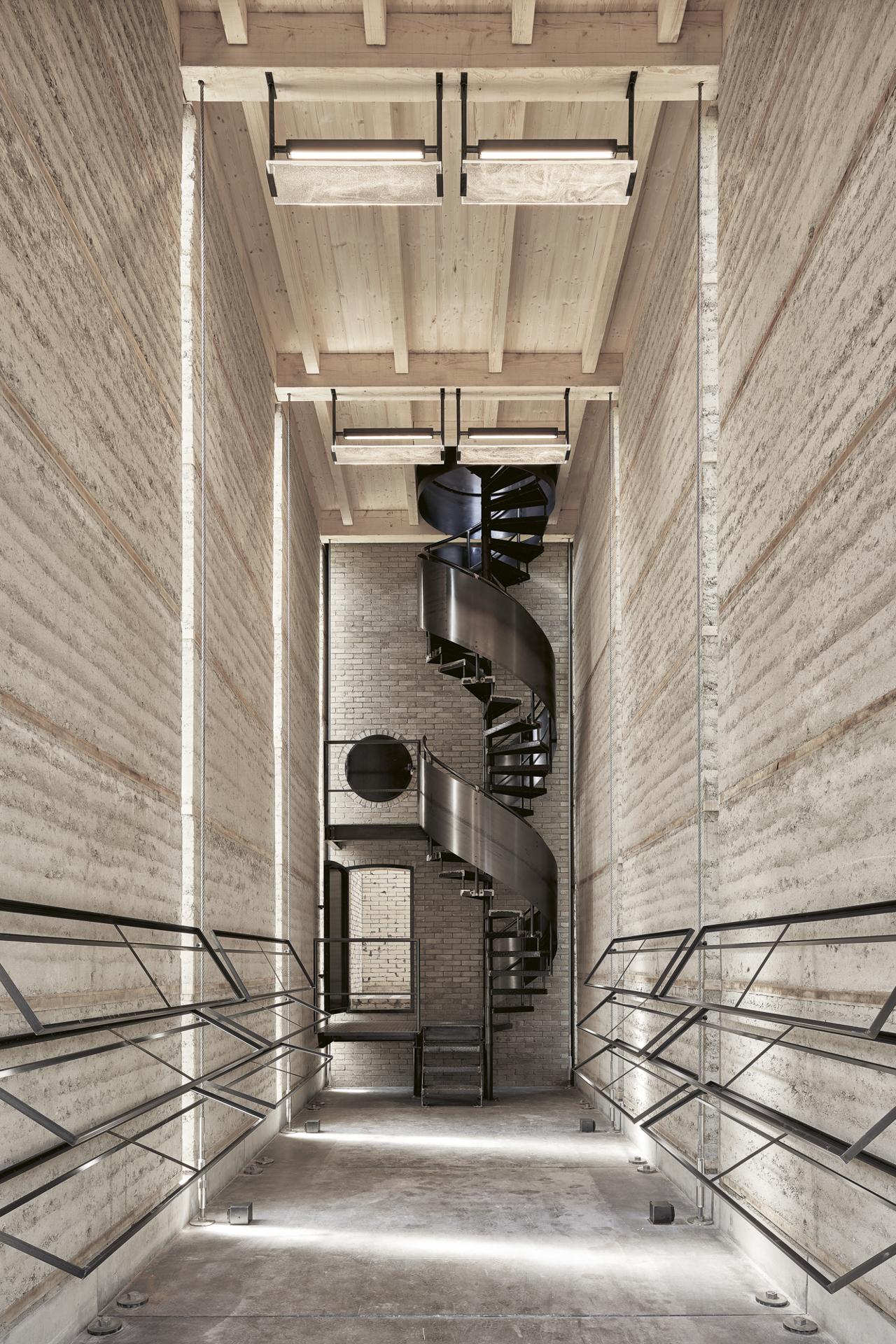
© Kuster Frey, Zurich
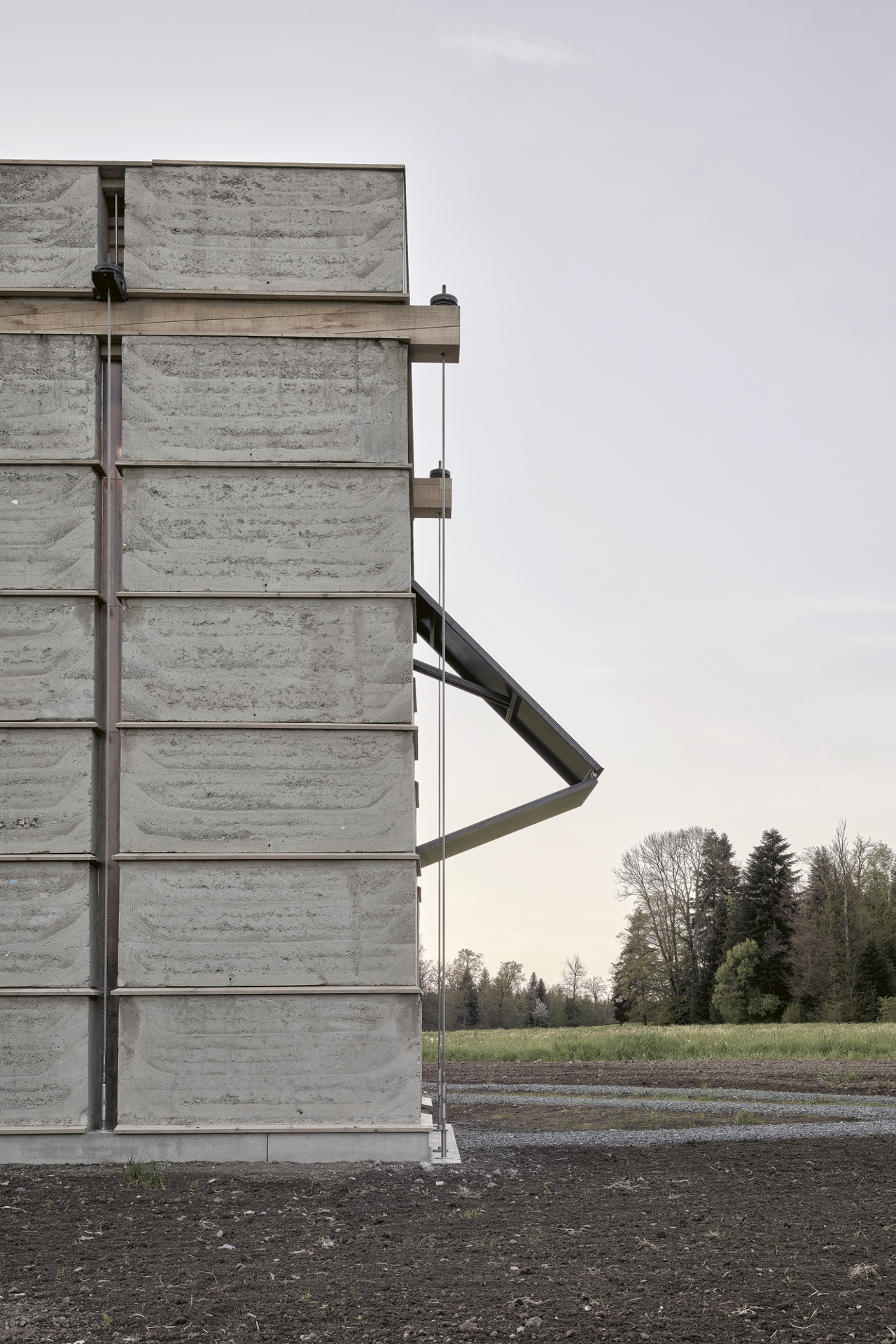
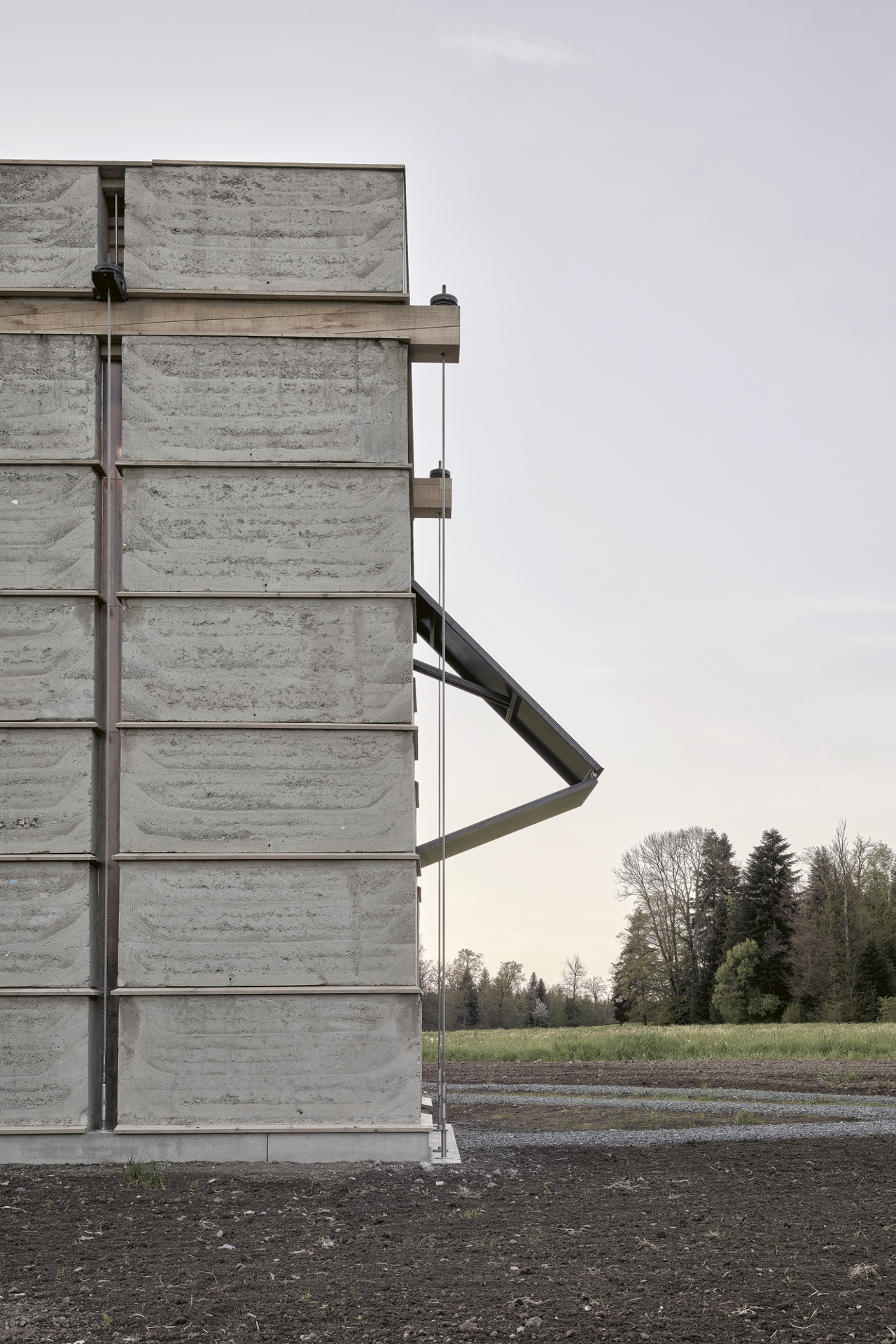
© Kuster Frey, Zurich
Lorem Ipsum: Zwischenüberschrift
They used a fat clay mixed with demolition rubble, as preparing the loam on-site would have been too time-consuming. A highlight of the project is how the earthen modules are stacked. Each element rests on the wooden plate on which it was compressed, which also facilitated the transport of the still soft rammed-earth blocks. One of the structure’s significant innovations was the integration of those base plates into the wall structure. Two grooves on the underside of each plate served as guides for tension cables. A weatherboard was mounted on each plate, which protects the earth from washing away and highlights the joining principle. Horizontal supports and corners made of trass lime mortar were pressed into the blocks as additional erosion protection.
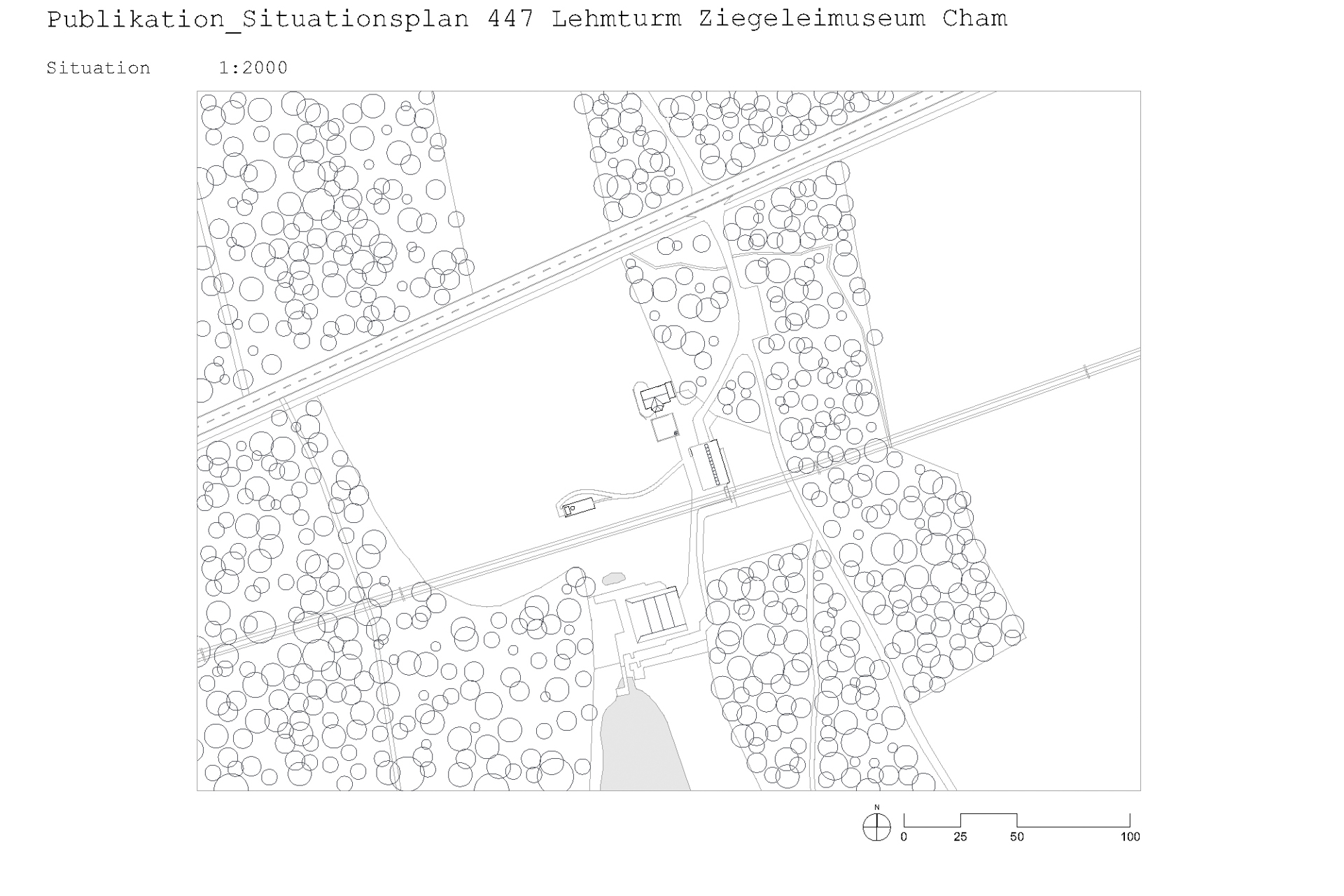
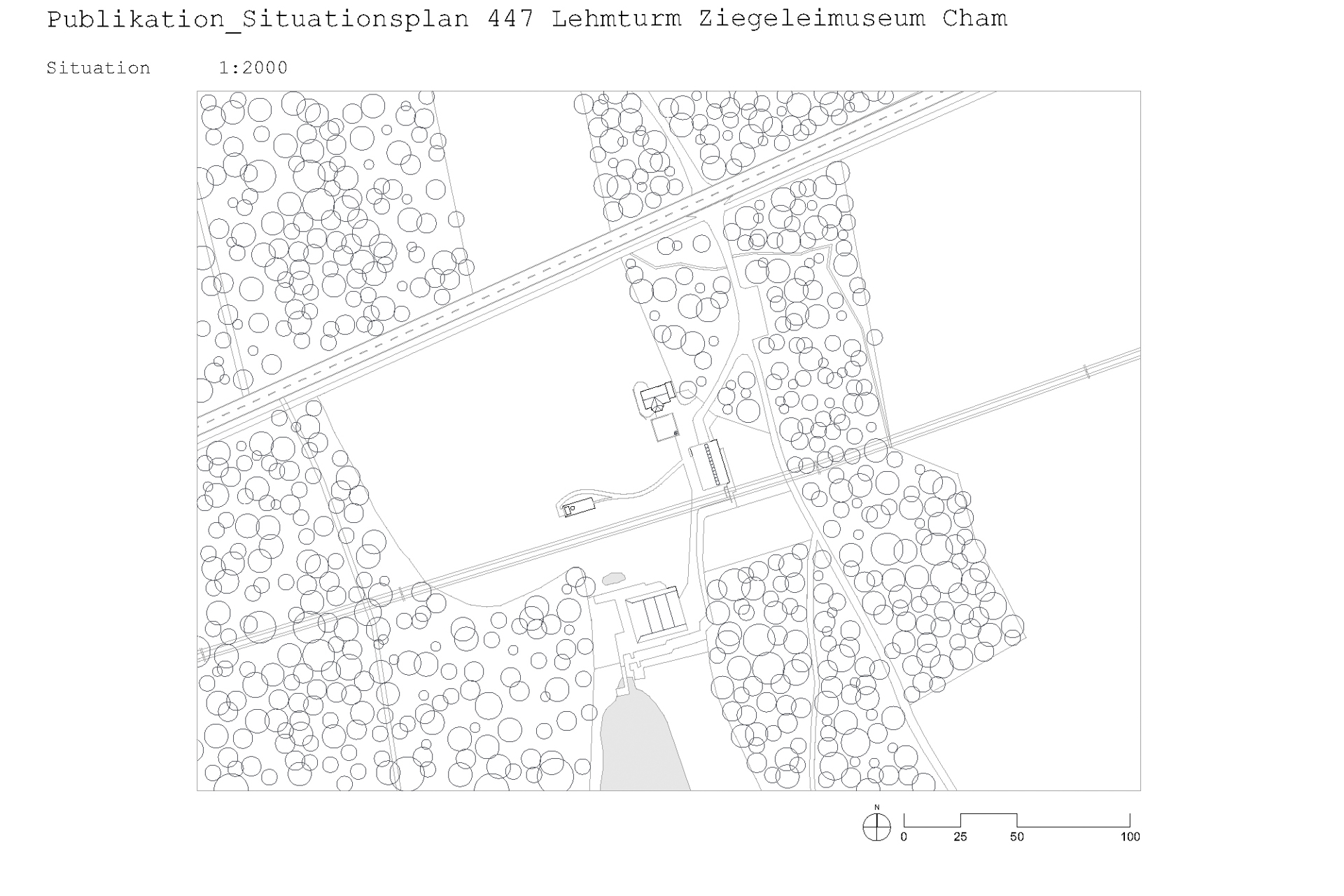
Situation plan – Graphic © Boltshauser Architekten
Lorem Ipsum: Zwischenüberschrift
One challenge in prestressed earthen construction is material creep and shrinkage, which can cause the prestressing tendons to loosen. To reduce these effects, the prefabricated rammed earth blocks used in Cham were allowed to dry for around a year, and additional steel springs in the prestressing tendons keep the pressure constantly high. Measurements have shown that the stability and hardness of the material increase under pressure. Further analyses will show whether this technology is suited for larger structures. Besides their purely technical function, the steel tendons lend a sense of rhythm to the compact structure – the construction becomes a design element.
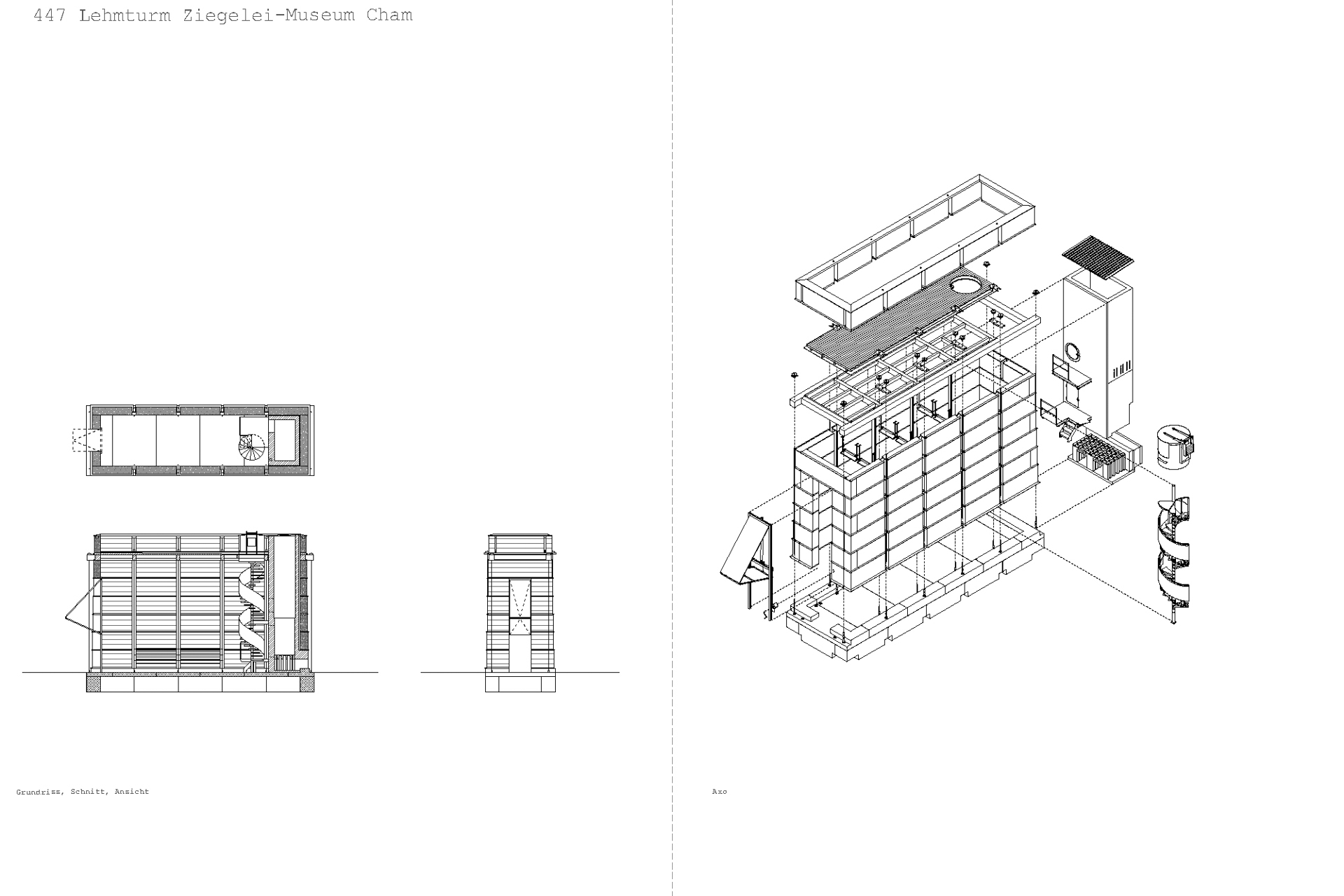
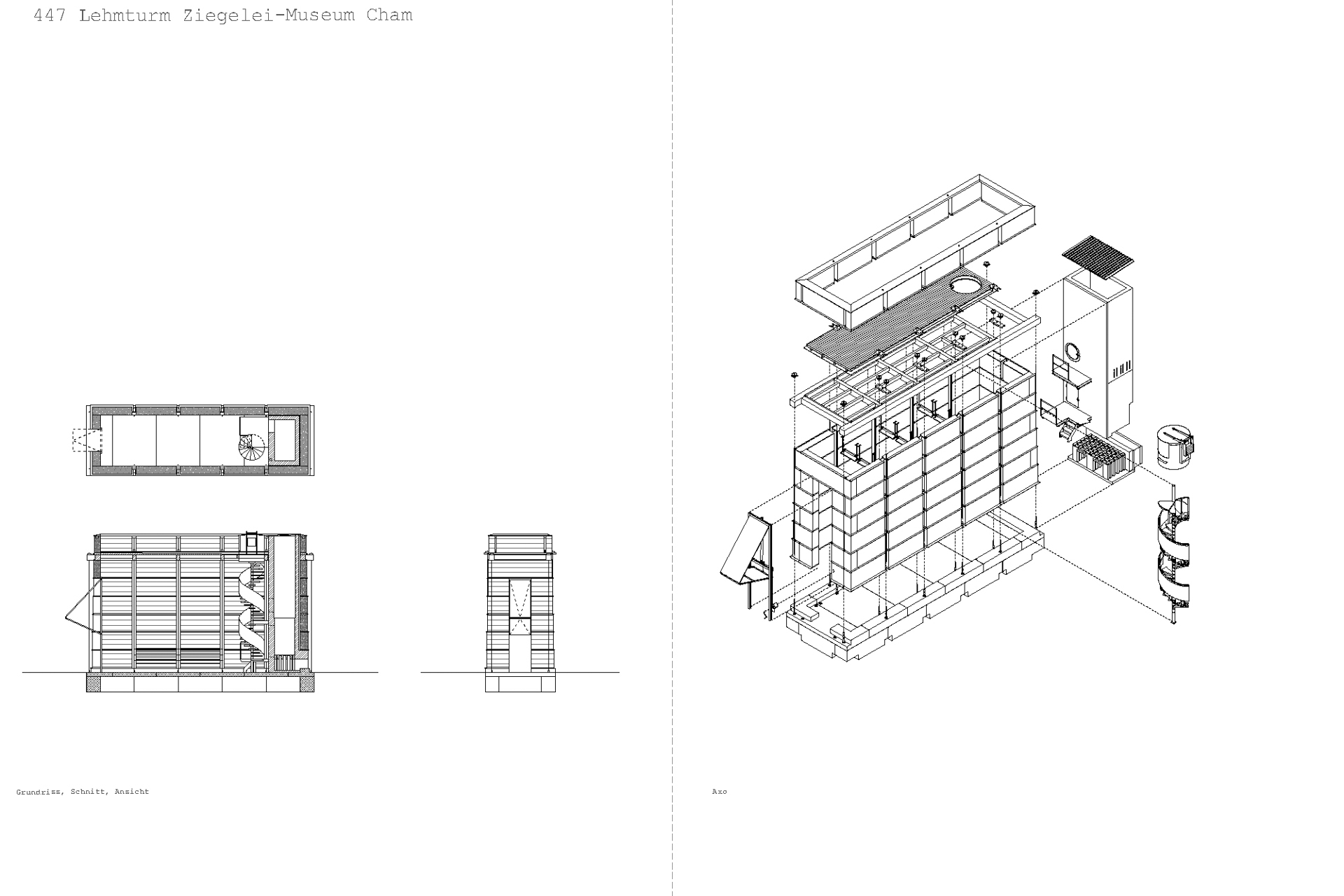
Floor plan, section, view, axonometry – Graphic © Boltshauser Architekten
Lorem Ipsum: Zwischenüberschrift
The interior opens to the ceiling, housing a showroom and a kiln for the employees to fire bricks. Light falls through the joints of the visibly layered earthen blocks. A spiral staircase of black steel, echoing the portal, leads up to the accessible roof. The structure was built on the condition that it must be dismantled after ten years. The rammed earth blocks can be easily reused or recycled – closing the loop in the material cycle and integrating the architecture into the circular economy.
Podcast: Interview with Roger Boltshauser
Read more in Detail 12.2022 and in our databank Detail Inspiration.
Architecture: Boltshauser Architekten
Client: Verein Ofenturm Ziegelei-Museum, Cham
Location: Ziegelhütte, 6332 Cham (CH)
Design: Robert Gentner, Regina Pötzinger, TU München
Further edited by: Demian Derron, Reto Habermacher, Johannes Koller, Georg Weilenmann, ETH Zürich
Statics: SEFROB
Lighting: Reflexion
Clay construction: LEHMAG, Brunnen, mit Studierenden verschiedener Hochschulen
Clay brickwork: Terrabloc
Clay material: Ziegelei Schumacher
Timber and metal construction: Nüssli
Post-tensioning: Jakob