High-bay warehouse made of natural materials
Weleda Cradle Campus in Schwäbisch Gmünd
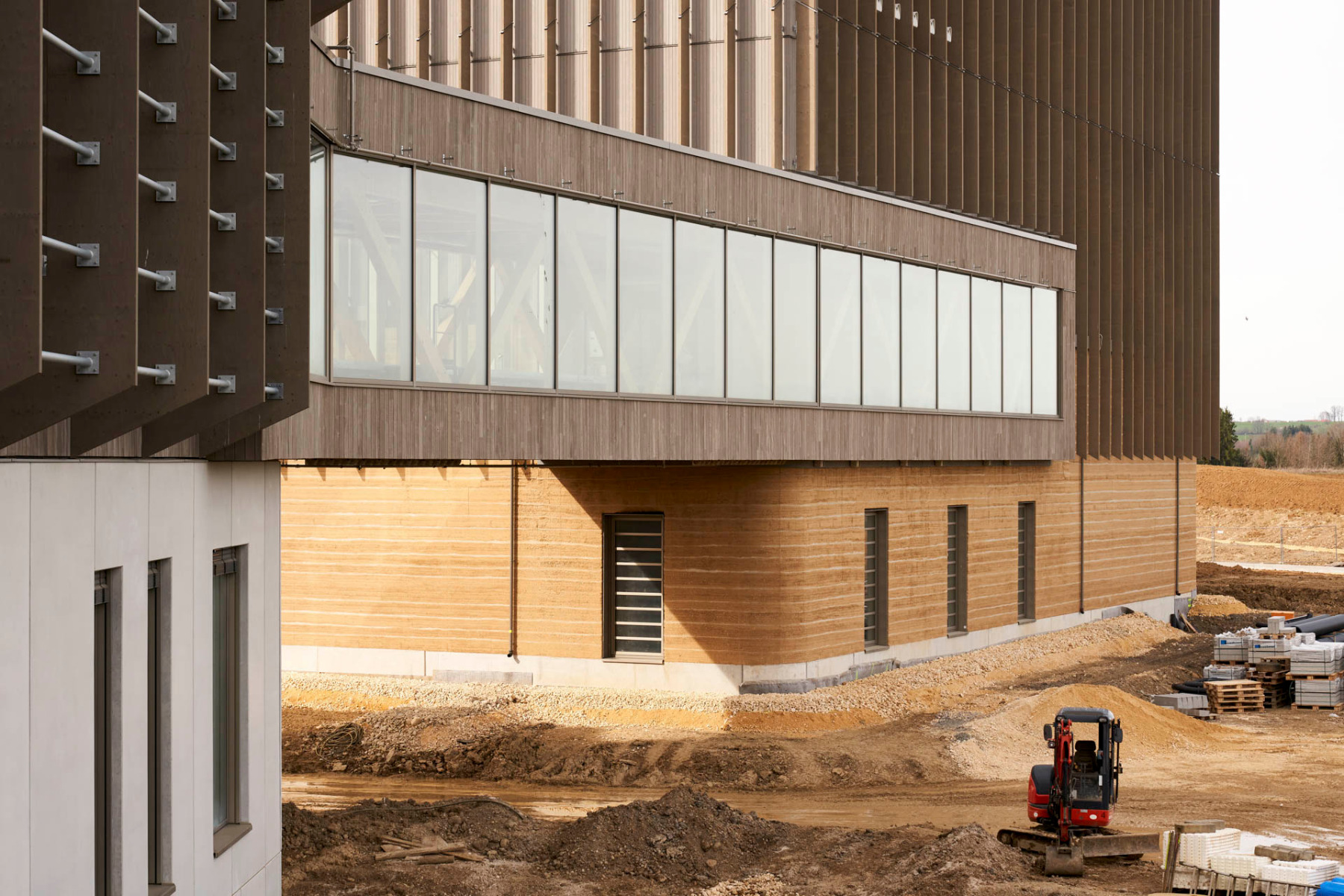
The clay for the 8-m-high rammed earth wall comes from the excavation pit. © Elias Hassos
As a manufacturer of natural cosmetics, there is a certain obligation to build sustainably, and this is what has been done on the "Gügling" on the outskirts of Schwäbisch Gmünd. This is where the new logistics centre for natural cosmetics manufacturer Weleda was built. The building has been pre-certified with the DGNB Platinum Standard and is carbon-neutral thanks to geothermal and solar energy. Natural materials were used as part of the sustainable building concept.
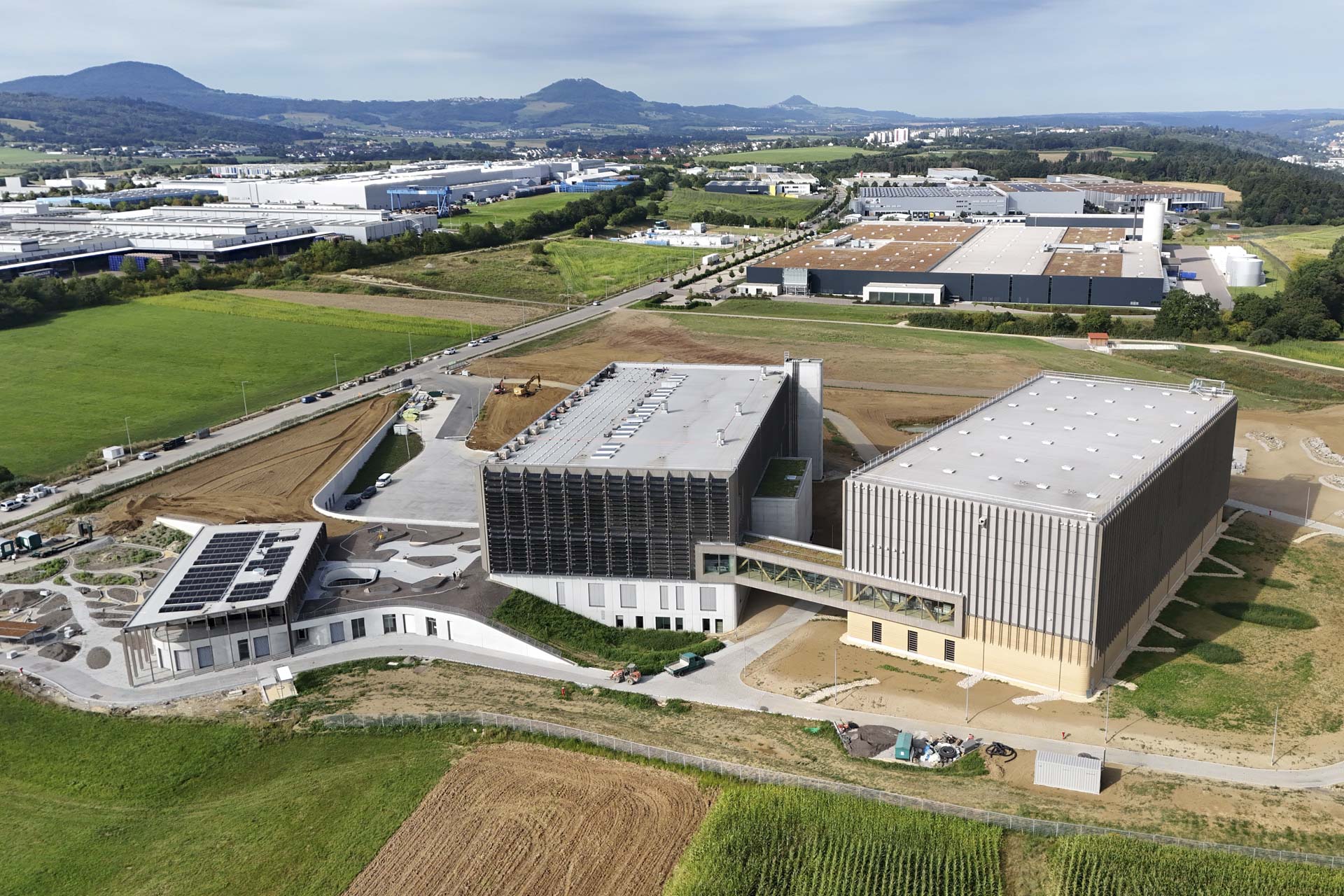
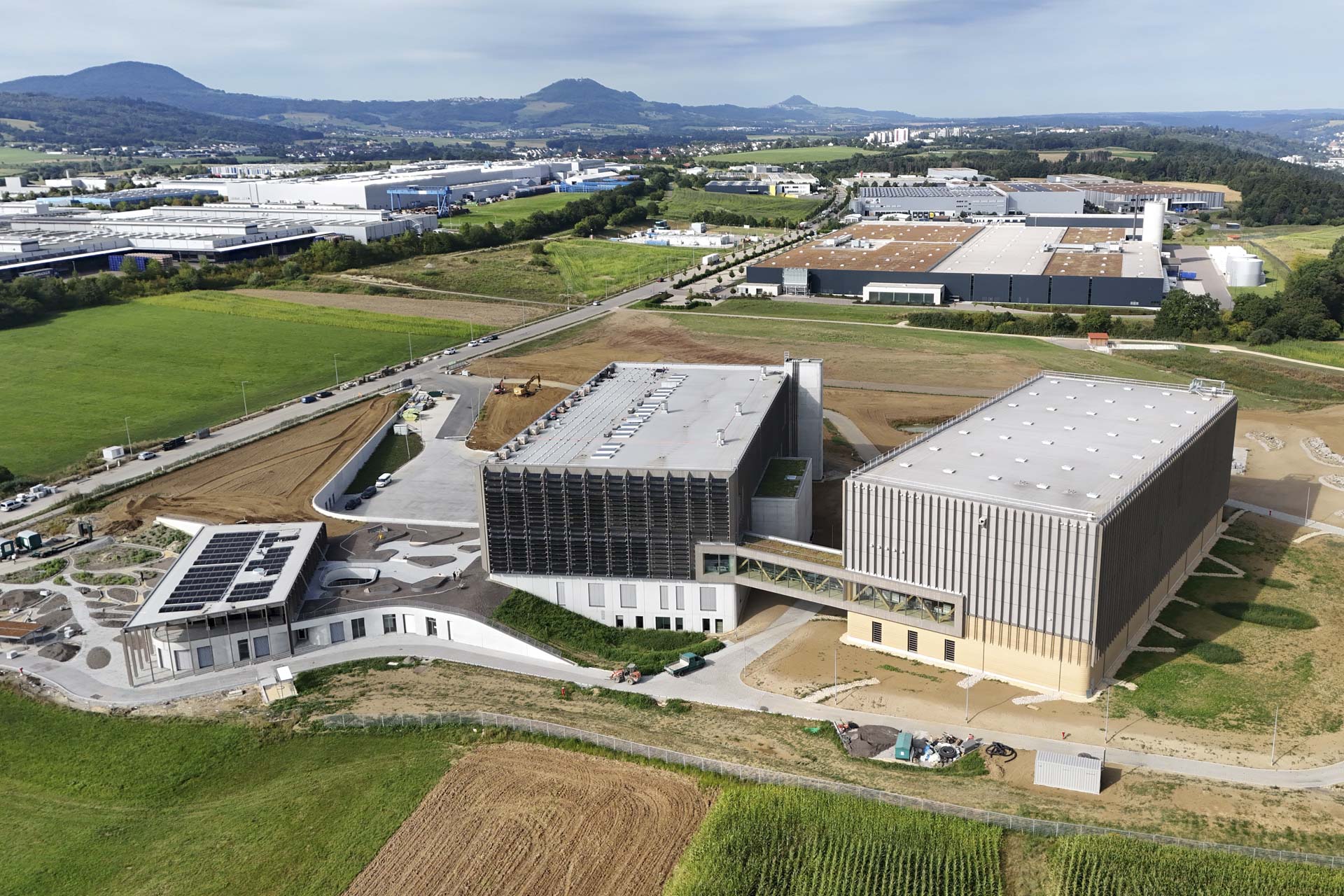
The logistics centre consists of three buildings: the recently completed high-bay warehouse (right) is connected by a bridge to the production building (centre) and the administration building (left). © Marco Licht
Everything in one place
The new building brings together the company's international distribution logistics, which were previously spread across six sites, in one central location. The integration of a fully automated high-bay warehouse with space for 17 200 pallets and the digitalisation of logistics has enabled Weleda to significantly optimise order picking and shipping. In the future, up to 10 000 deliveries to 47 countries will be made from here every day.
Natural materials in use
The recently inaugurated high-bay warehouse, which was completed in the summer of 2024, is the largest continuous rammed-earth building in Germany, measuring 81 x 38 m. It is one of three new buildings on the 72 000 m² site, along with a production building and an administrative building. The cube sits on a reinforced concrete trough 5 m deep in the ground. Above it is an 8-m-high and 60-cm-thick rammed earth plinth, which regulates the humidity inside. The clay comes from the excavation pit and has been mixed with local gravel in a ratio of 1:3. Above the rammed earth walls, the 26 m high building envelope continues as an insulated timber facade. The combination of different construction elements is designed to ensure that the building does not need to be heated or cooled in order to store the temperature-sensitive cosmetics and medicines in the best possible way.
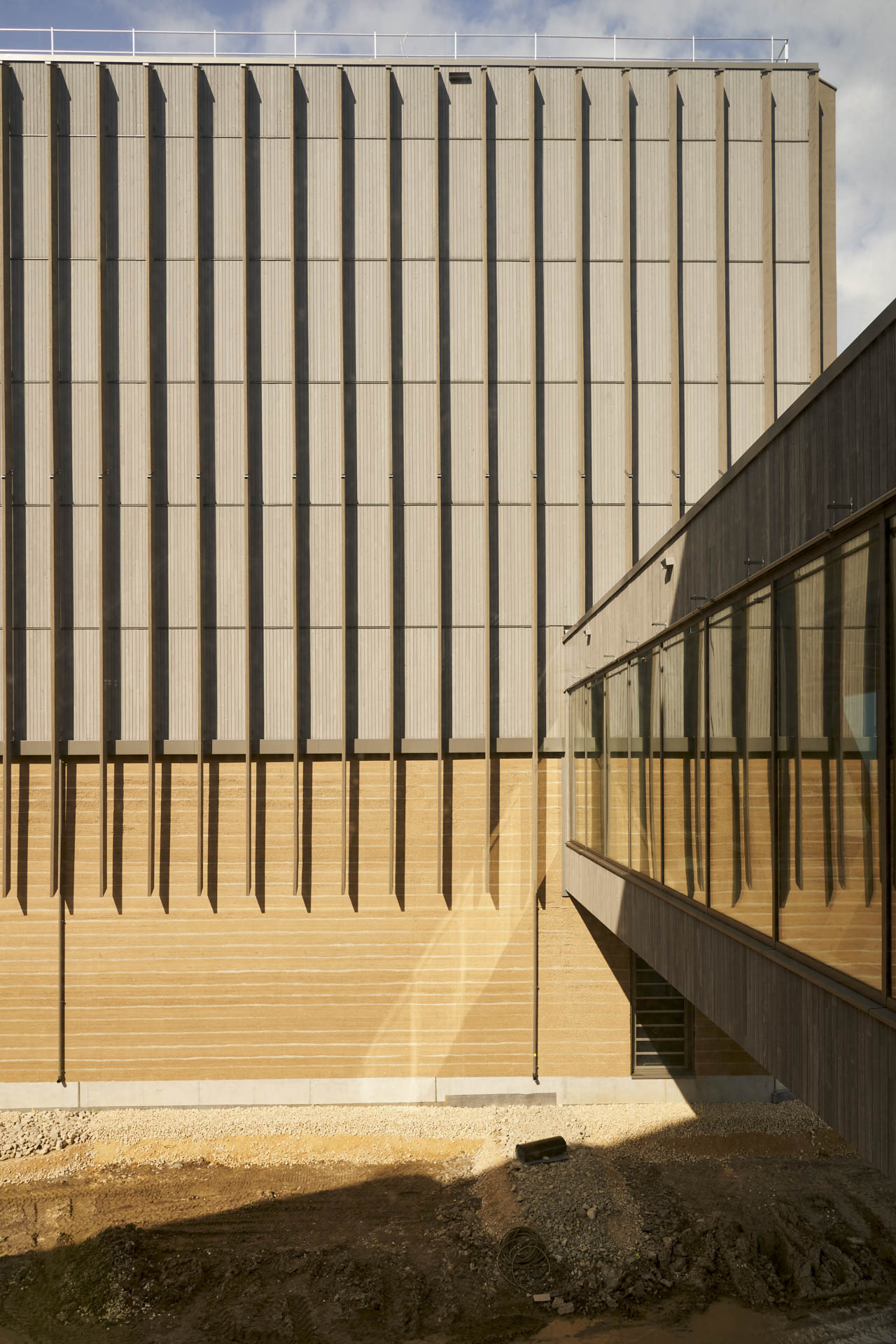
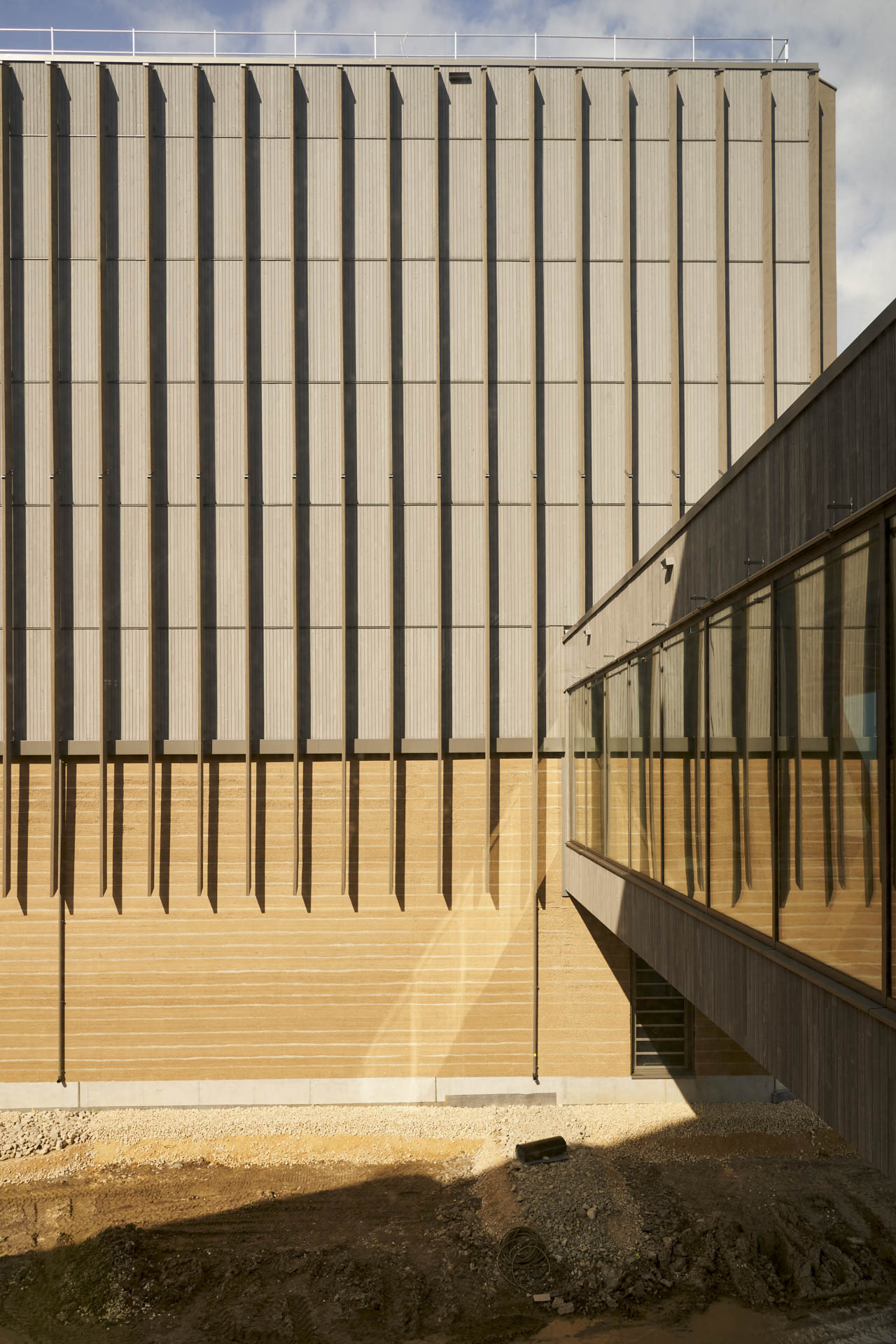
High-bay warehouse with bridge, © Elias Hassos
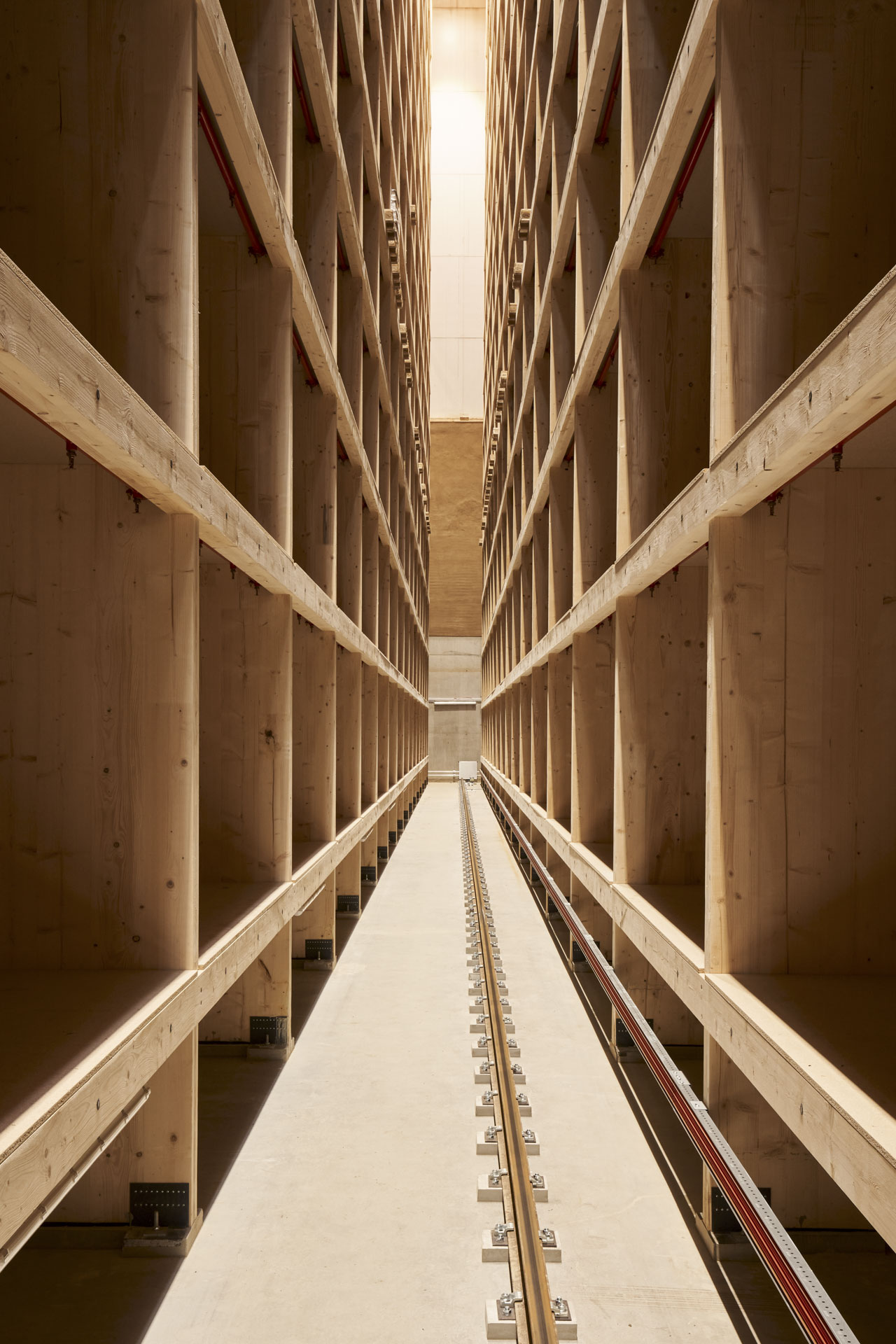
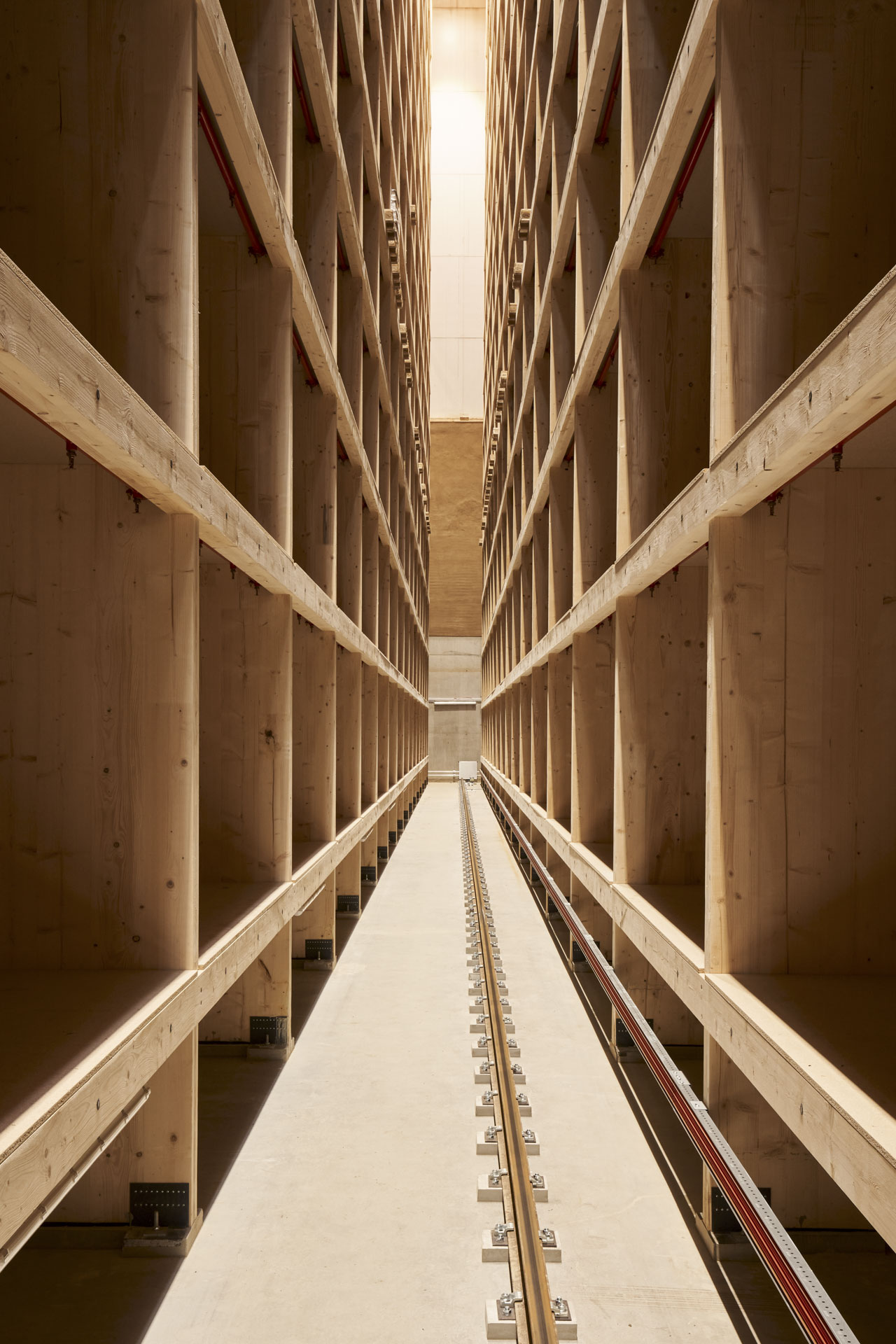
View of the high-bay warehouse, © Elias Hassos
Consistently sustainable
Only 20 percent of the site was built on for the new logistics centre; the rest was renaturalised and landscaped with native plants and orchards. Weleda relies entirely on renewable energy to power the logistics centre. The heating and cooling requirements can be met 100 percent by geothermal energy and solar power. This is made possible by 48 geothermal probes at a depth of 140 m and a sophisticated solar system with around 10 000 photovoltaic modules on the roofs and facades. The PV system generates approximately 1.3 GWh of electricity per year. The system saves about 207 tons of CO₂ per year. Although construction costs were about 50 percent higher due to the elimination of fossil fuels such as gas, the investment is expected to pay for itself within 12 to 14 years. In addition, waste heat from the cooling systems is used to regenerate the geothermal field in the summer, further increasing efficiency.
Architecture: Michelgroup
Client: Weleda Immobilien GmbH
Location: 73525 Schwäbisch Gmünd (DE)
Team: Nico Santuario, Tina Bauer, Carmen Saur
Structural planning for rammed earth, specialist planning for earth building: ZRS Ingenieure
Structural engineering reinforced concrete: Bauer + Partner
Structural engineering timber construction / HBW: Merz Kley Partner
HVAC planning: IP – Innovatives Planen
Electrical planning: Ott Ingenieure
Landscape architecture: Büro Hink Landschaftsarchitektur
Energy planning: Transsolar Energietechnik
Building physics: BBI Bayer Bauphysik Ingenieurgesellschaft
Fire prevention: TÜV Süd Industrie-Service
Transport facilities: Pirker + Pfeiffer ingenieure
Site management: Michelgroup
Property size: 72 000 m²
Total effective floor area: 14 700 m²
Gross floor area: 18 700 m²
Gross cubic capacity: 198 250 m³
Completion: 2024
Certification: DGNB Platin (pre-certified)