// Check if the article Layout ?>
Toward CO2 neutrality
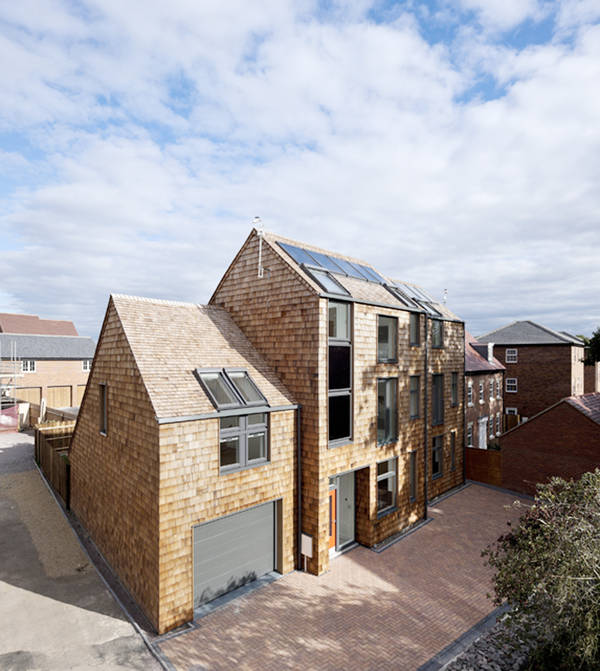
Great Britain has four more years to go before all new housing in the country has to be CO2 neutral. How this could work is demonstrated by 'CarbonLight Homes', a semi-detached house in Rothwell designed by London based HTA Architects.
The CarbonLight Homes in Rothwell (Northamptonshire) are the last of a current series of 'Model Homes 2020' projects. Since 2009, six buildings in five European countries have been realised by Velux, the roof window manufacturer, with the aim of combining CO2 neutrality with high living comfort. These include four new residential buildings, one administrative building and a renovation of a residential building.
The marketability of the CarbonLight Homes was of prime importance to the client: the semi-detached house designed by HTA Architects (London) is not located on a university research campus, but right in the middle of a development area with over 200 houses, currently being realised by project developer Bovis Lend Lease. The typology of the design is based on typical British terraced housing: narrow street fronts in combination with large building depths permit maximum utilisation of the often deep plots of land and minimisation of the area of the building envelope exposed to the outside climate. The living space layout also corresponds closely to what is offered by the average new British housing: one half of the house has three rooms on an area of 97 m²; the other half has four rooms on 142 m².
The marketability of the CarbonLight Homes was of prime importance to the client: the semi-detached house designed by HTA Architects (London) is not located on a university research campus, but right in the middle of a development area with over 200 houses, currently being realised by project developer Bovis Lend Lease. The typology of the design is based on typical British terraced housing: narrow street fronts in combination with large building depths permit maximum utilisation of the often deep plots of land and minimisation of the area of the building envelope exposed to the outside climate. The living space layout also corresponds closely to what is offered by the average new British housing: one half of the house has three rooms on an area of 97 m²; the other half has four rooms on 142 m².
The CarbonLight Homes are not intended to be model 'show' houses, but will be occupied by two test families in the next months, and then sold on the free market. The results of extensive monitoring of the dwelling during the test phase will permit Velux to draw conclusions about the functionality and user-friendliness of the highly efficient buildings.
Energy concept
The favourable energy balance is based on a highly insulated building envelope, with U-values of 0.11 W/m²K 'all round' (including floor plate). Daylight is a significant factor contributing to the energy balance as well as user liveability: the window areas of the structure make up almost 25% of the floor area. An average daylight factor of 5 per cent could therefore be achieved in every room of the two houses (except the garage). This is more than three times the figure specified for new housing in Great Britain by the Code for Sustainable Homes.
The key element of the lighting (and ventilation) strategy are the two multi-storey, open living and access areas occupying the entire height of the building all the way up to the apex. Purely natural ventilation and infiltration are driven by the resulting stack effect. A ventilation system with heat recovery was not installed. In summer, these atria allow efficient automated cooling of the building with night air, with the help of a window control system.
The heat required by the new building is obtained from two sources: solar heat collectors and an air/water heat pump, each supplying about half the basic demand. Biomass stoves are provided for extra heating on very cold winter days.
The favourable energy balance is based on a highly insulated building envelope, with U-values of 0.11 W/m²K 'all round' (including floor plate). Daylight is a significant factor contributing to the energy balance as well as user liveability: the window areas of the structure make up almost 25% of the floor area. An average daylight factor of 5 per cent could therefore be achieved in every room of the two houses (except the garage). This is more than three times the figure specified for new housing in Great Britain by the Code for Sustainable Homes.
The key element of the lighting (and ventilation) strategy are the two multi-storey, open living and access areas occupying the entire height of the building all the way up to the apex. Purely natural ventilation and infiltration are driven by the resulting stack effect. A ventilation system with heat recovery was not installed. In summer, these atria allow efficient automated cooling of the building with night air, with the help of a window control system.
The heat required by the new building is obtained from two sources: solar heat collectors and an air/water heat pump, each supplying about half the basic demand. Biomass stoves are provided for extra heating on very cold winter days.
The CarbonLight Homes have a primary energy demand of about 85 kWh/m²a , including the power required for the entire household. Most of this is covered by the energy generated by the heat pump and solar collectors, which amounts to 66 kWh/m²a. The missing 19 kWh/m2a – equivalent to 8 kg CO2 emissions - are compensated by a kind of offset trading customary in Great Britain: Velux invested in the renovation measures on existing buildings in the neighbourhood. The CO2 emissions of the CarbonLight Homes are even overcompensated by the annual energy savings achieved by these.
Construction
The new buildings covered with wood shingles are supported by a steel frame structure. The roof areas are composed of structural insulated panels, with a thickness of 235 millimetres. This is a self-supporting type of sandwich panel with a PIR insulation core covered with OSB boards on both sides, typically used in Great Britain. The outer walls are a light steel frame construction infilled with mineral wool and covered with 130 mm of expanded plastic slabs on the outside for additional insulation. The total thickness of the insulation of the outer walls is 230 millimetres.
The new buildings covered with wood shingles are supported by a steel frame structure. The roof areas are composed of structural insulated panels, with a thickness of 235 millimetres. This is a self-supporting type of sandwich panel with a PIR insulation core covered with OSB boards on both sides, typically used in Great Britain. The outer walls are a light steel frame construction infilled with mineral wool and covered with 130 mm of expanded plastic slabs on the outside for additional insulation. The total thickness of the insulation of the outer walls is 230 millimetres.