Produced using a 3D printer
Oregon Dragon Bench by Joris Laarman
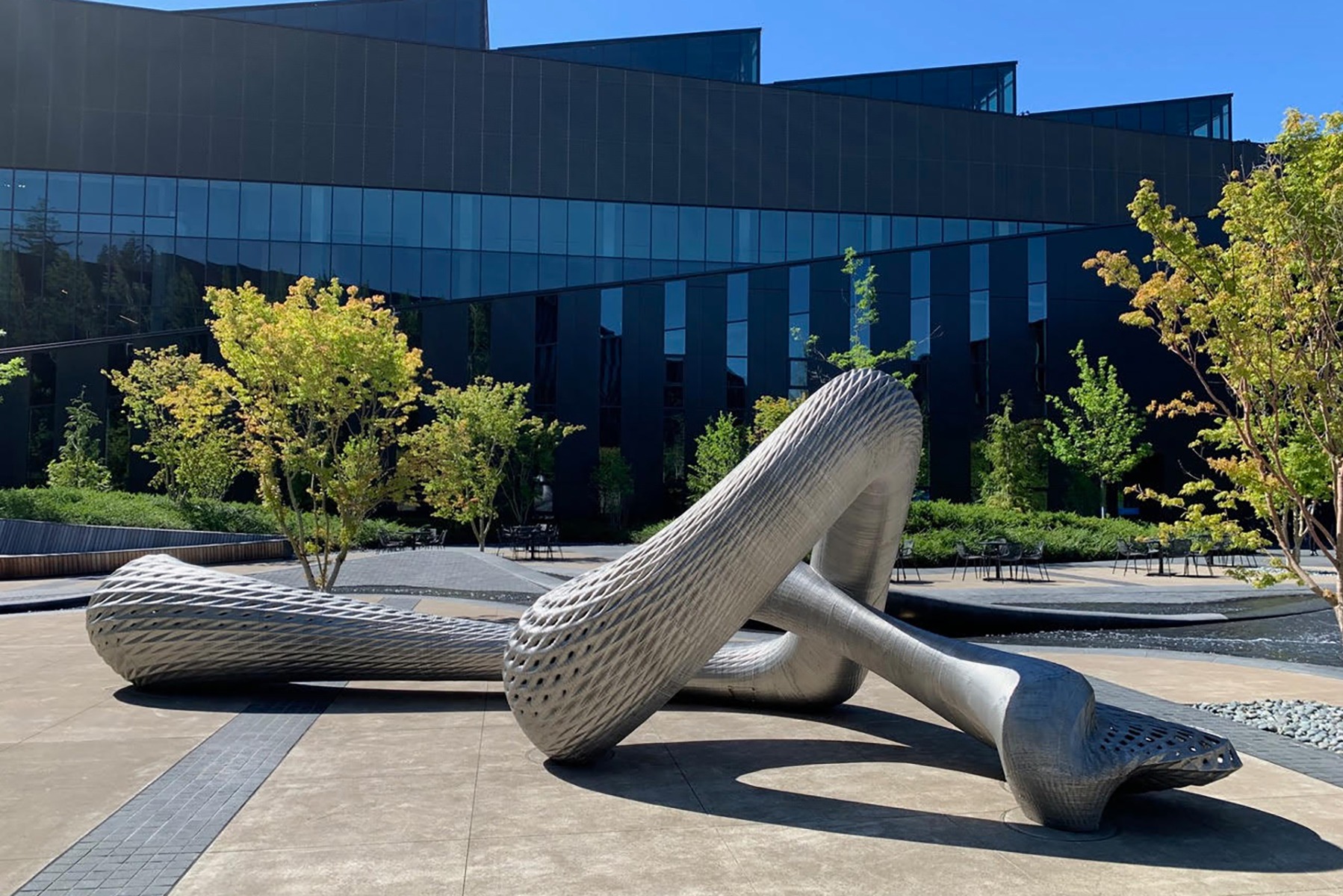
© Nike Oregon Dragon Bench, Design Joris Laarman Lab, Manufactured by MX3D
The Dutch designer Joris Laarman has devised a 10 m sculptural bench for the Nike Campus in the U.S. state of Oregon. The object was produced in stainless steel with the help of a 3D printer. Laarman created his first „Dragon Bench“ in 2014 and the same year it was produced by the Dutch company MX3D, as also applies to the Oregon Dragon Bench.
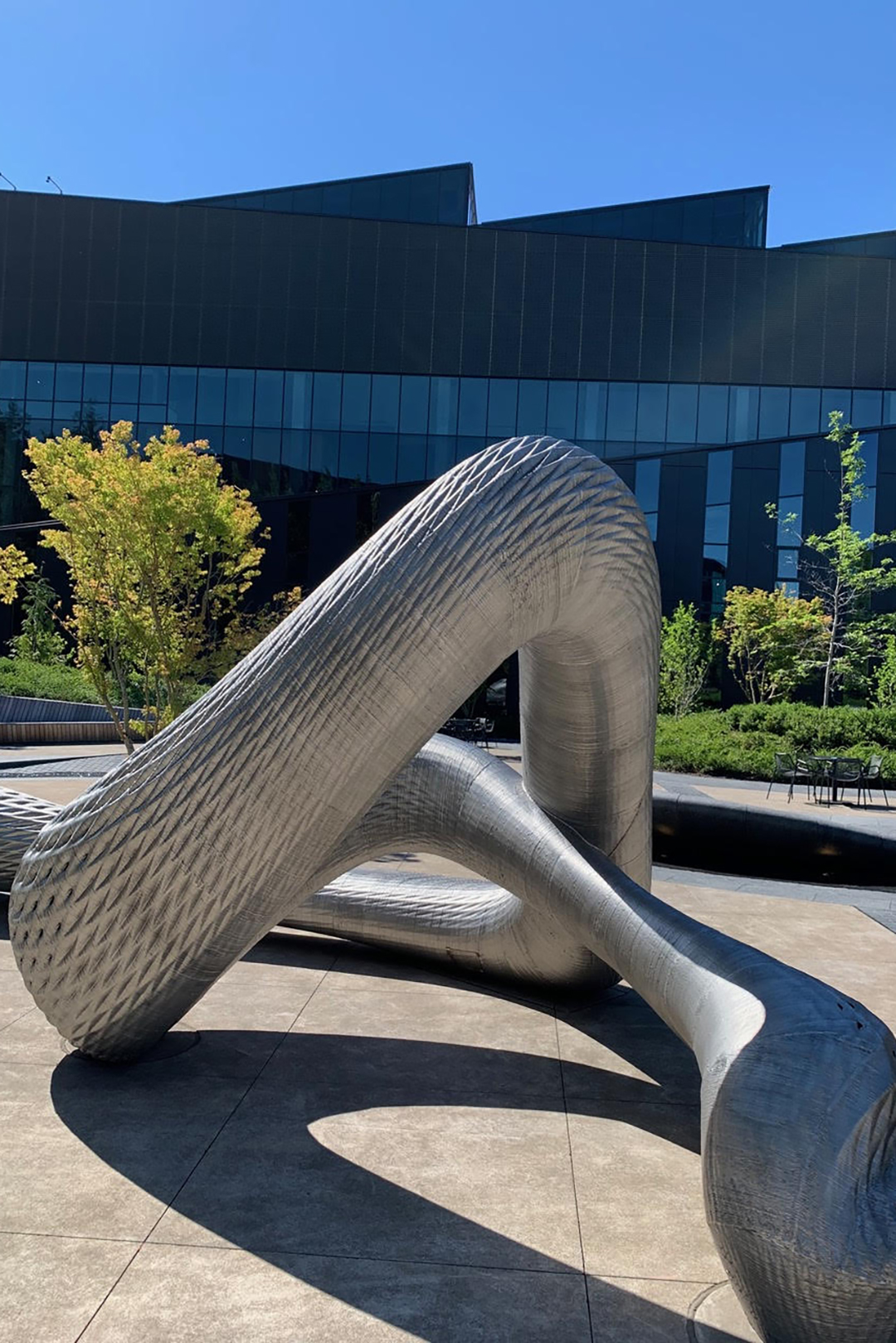
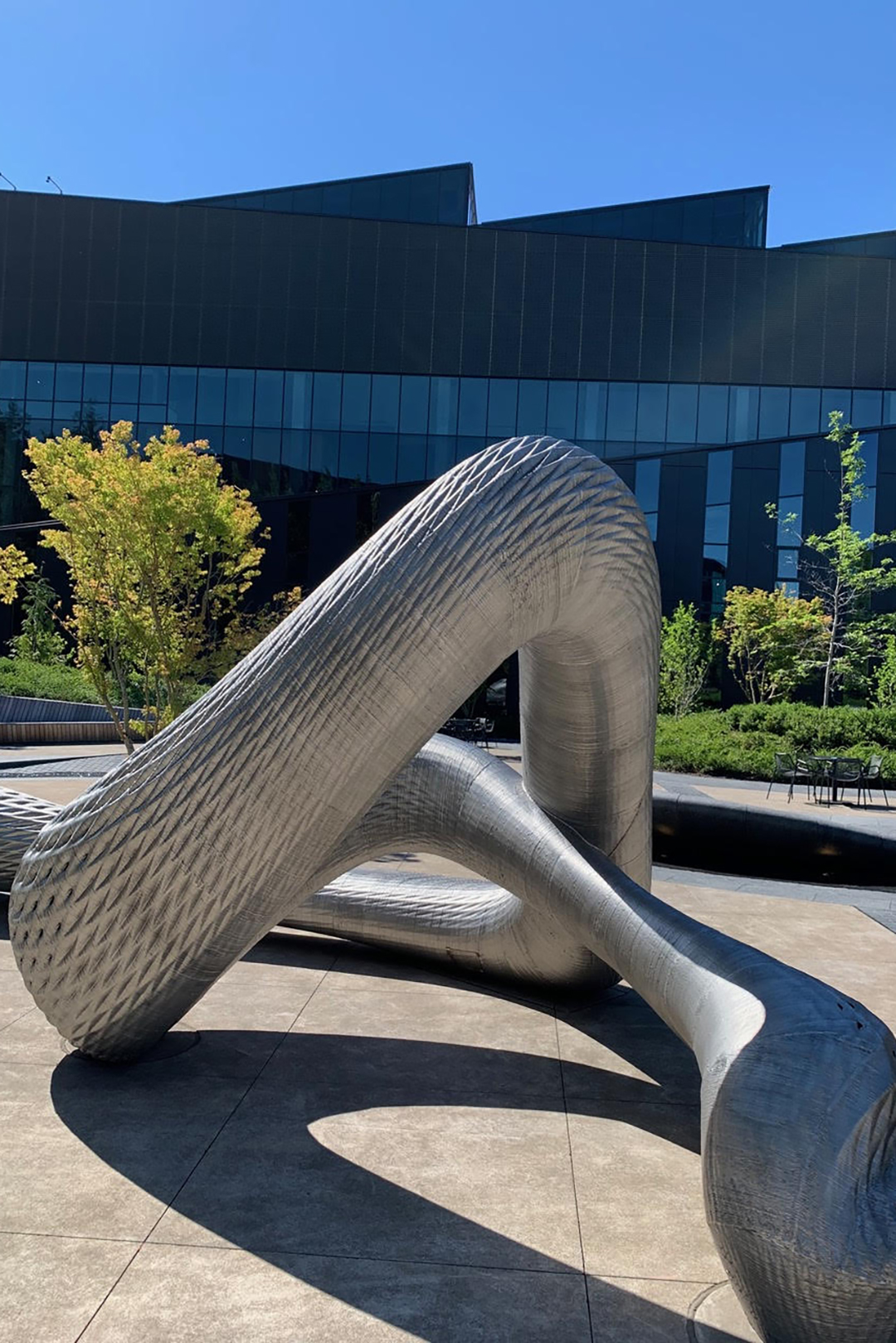
© Nike Oregon Dragon Bench, Design Joris Laarman Lab, Manufactured by MX3D
Lorem Ipsum: Zwischenüberschrift
In an unprecedented step, MX3D had combined an industrial robot with a welding machine to fabricate a three-dimensional object point by point in the 3D printing process. Using the same method – known as Robotic Wire Arc Additive Manufacturing WAAM) – MX3D has since printed a 12 m footbridge over a canal in Amsterdam that saw its inauguration in the summer of 2021.
Lorem Ipsum: Zwischenüberschrift
Dragon Benches produced to date are generally museum pieces found at such places as the High Museum of Art in Atlanta, the Houston Museum of Fine Arts and the Museum in Groningen. The case regarding the Oregon Dragon Bench is fundamentally different, the seat having been installed at an open space in front of Nike’s Advanced Innovation Centre in Beaverton in the U.S. state of Oregon. It thus had to be hard-wearing and capable of withstanding misuse.
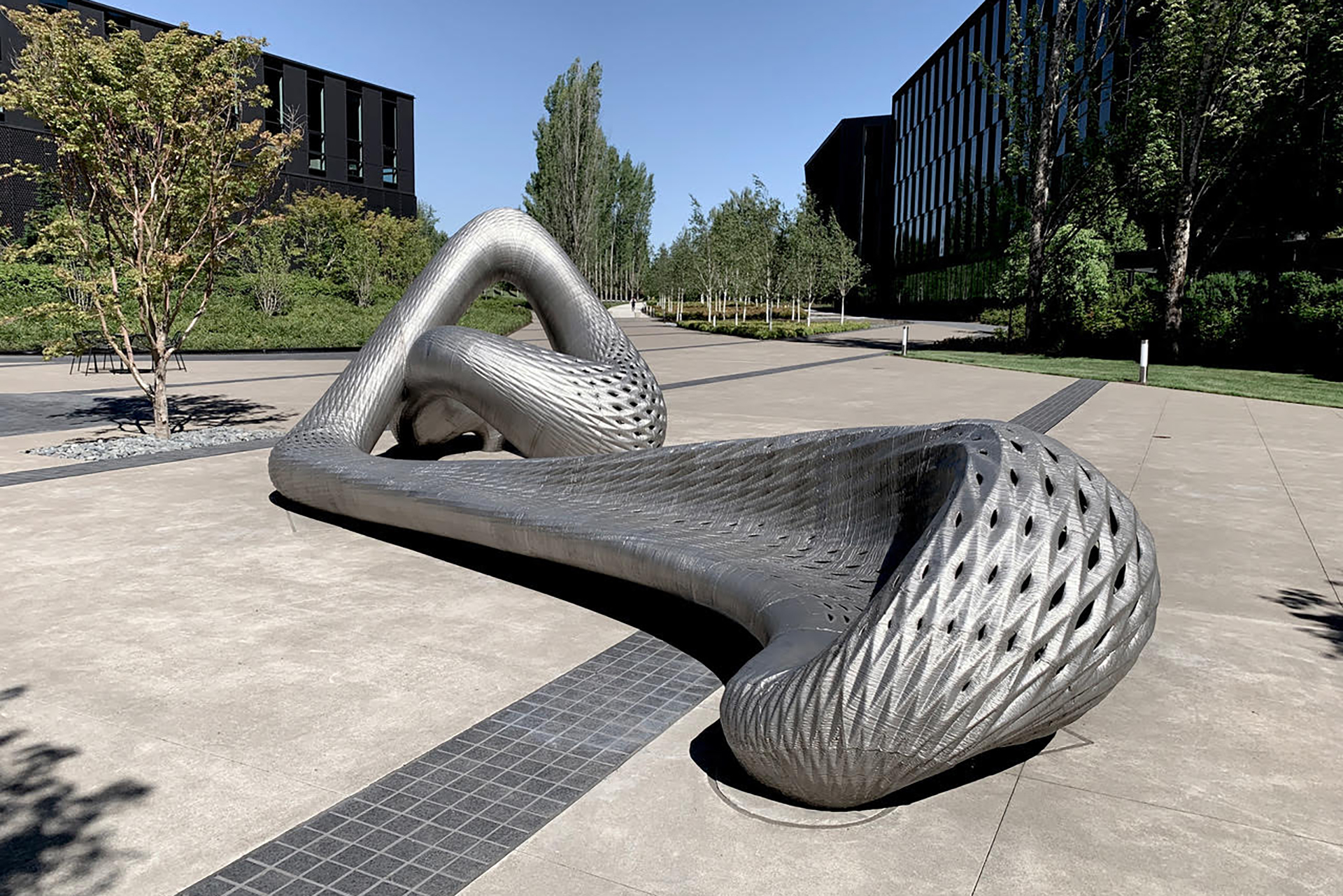
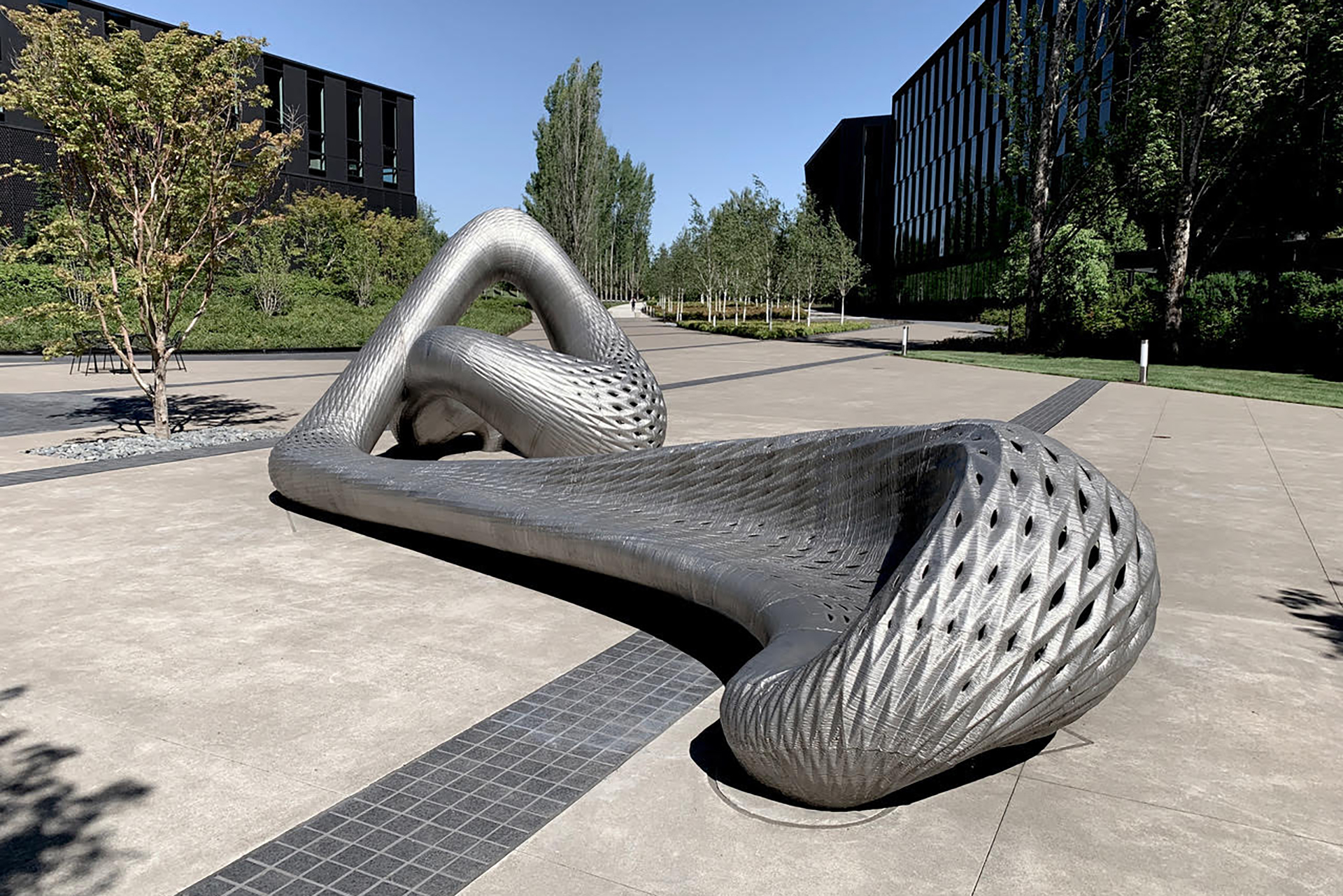
© Nike Oregon Dragon Bench, Design Joris Laarman Lab, Manufactured by MX3D
Lorem Ipsum: Zwischenüberschrift
The metal structure in this model is also a significant improvement over the first Dragon Bench, being denser wherever structural stability is required, whereas the 3D printer applied less material in areas involving a lower load demand. The bench, which was produced in duplex stainless steel, is 10 m long, 3 m wide and 2 m high and consists of segments varying in length between 1 m and 2,5 m and were welded together on site. According to MX3D, an optimized welding robot applies about 1 to 4 kg of steel per hour in the WWAM process, making it, as the manufacturer states, one of the fastest printing process for metals and also the most flexible, thanks to the movable robot arm.
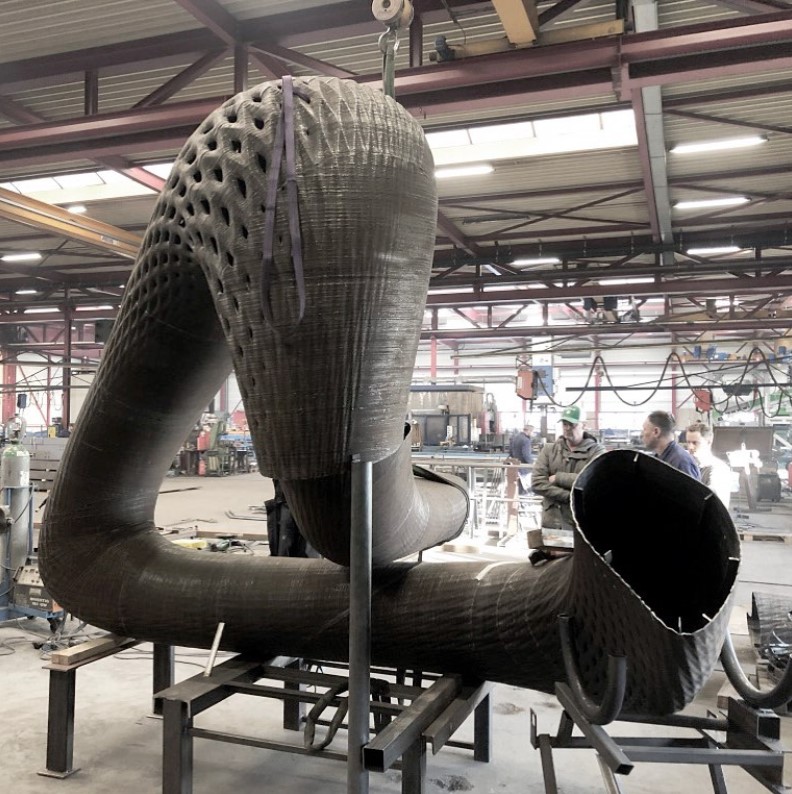
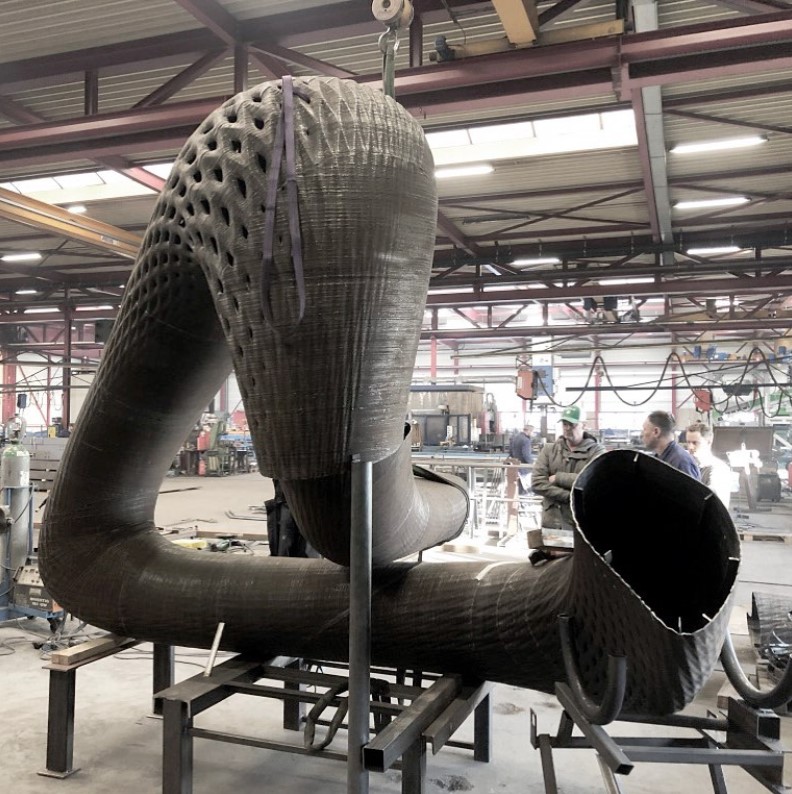
© Nike Oregon Dragon Bench, Design Joris Laarman Lab, Manufactured by MX3D
The fact that MX3D uses standard welding wires in production instead of more pricey metal powder cuts down on costs. In a life-cycle assessment of 3D printing conducted by Delft Technical University for MX3D, the approach was compared to other processing methods such as metal casting and CNC milling. WAAM proved advantageous in all cases involving both statical optimisation of the shape of the print object at the design phase and a respectively lightweight structure, thus requiring less material to be used. According to MX3D, the welding robot consumes significantly less energy than 3D printing processes, which use laser beams to construct objects layer for layer in a tub filled with metal powder.
Design: Joris Laarman Lab
Manufacture: MX3D
Location: Nike Campus, Beaverton (US)
AAA: A