Digital Gothic
HiRes Concrete Slab in the Empa NEST Dübendorf
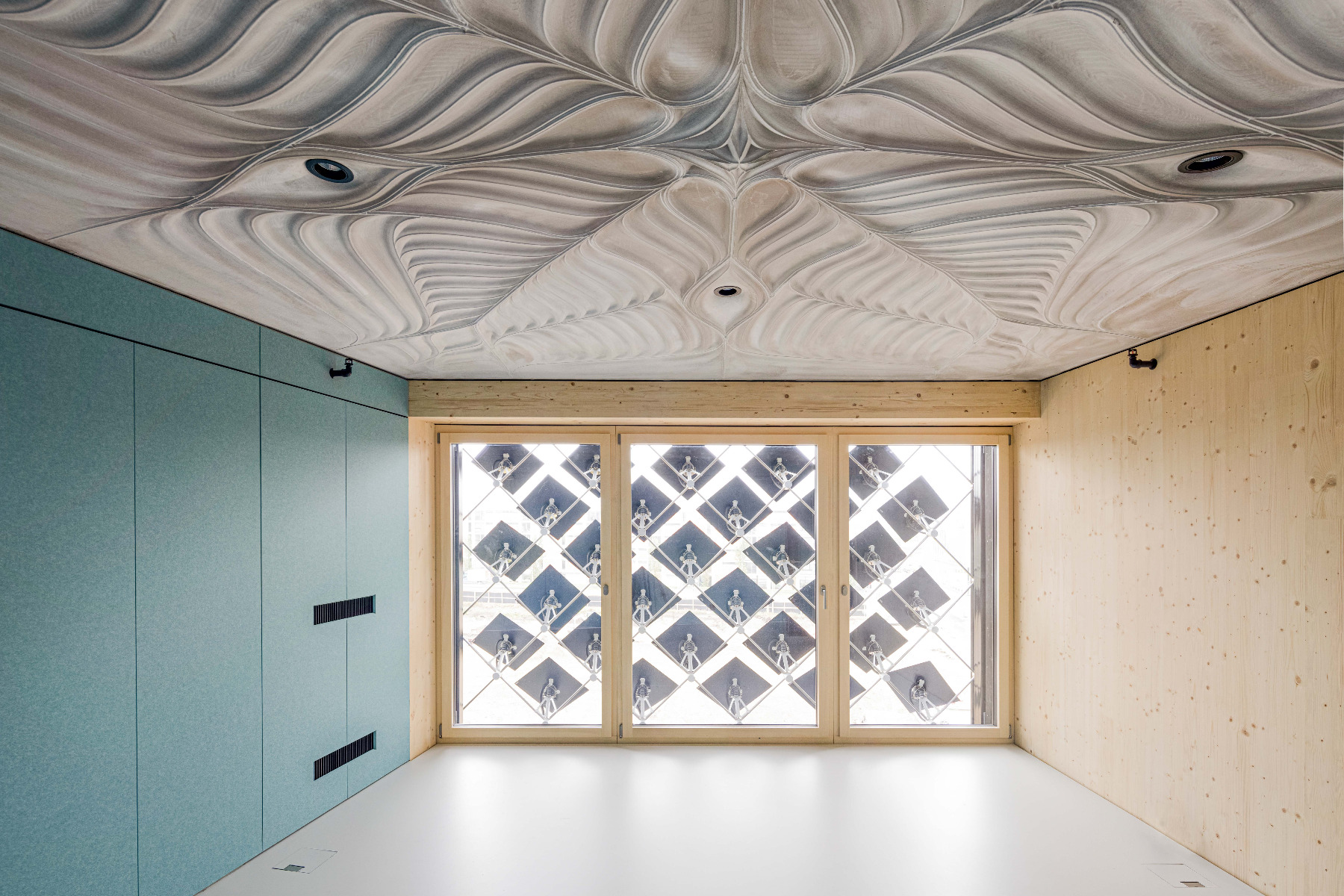
© Andrei Jipa
Centuries of experience led the architects of the Gothic period to design shapes that were both efficient and aesthetically convincing. Nowadays, computer-aided structural optimization processes often lead to similar results.
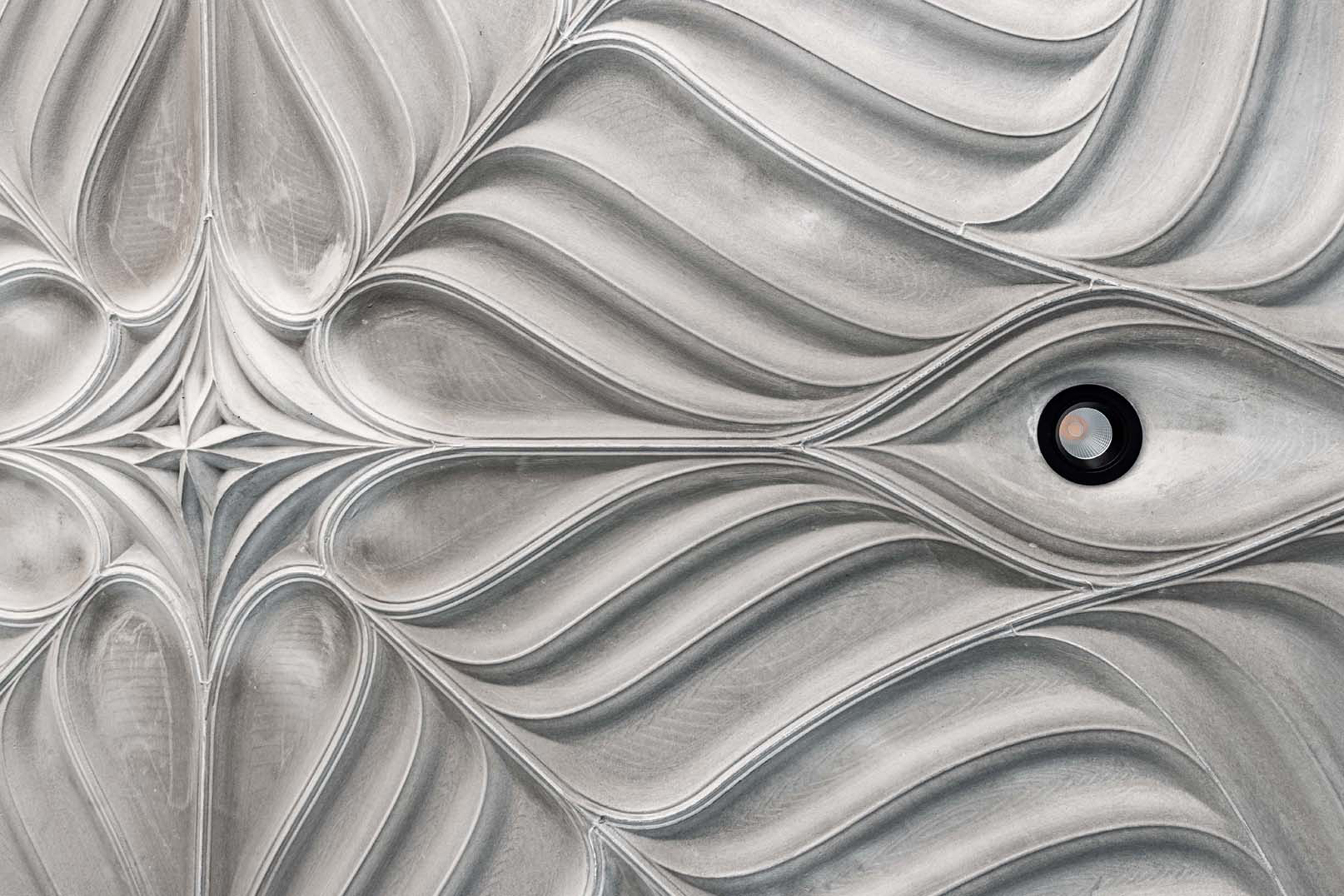
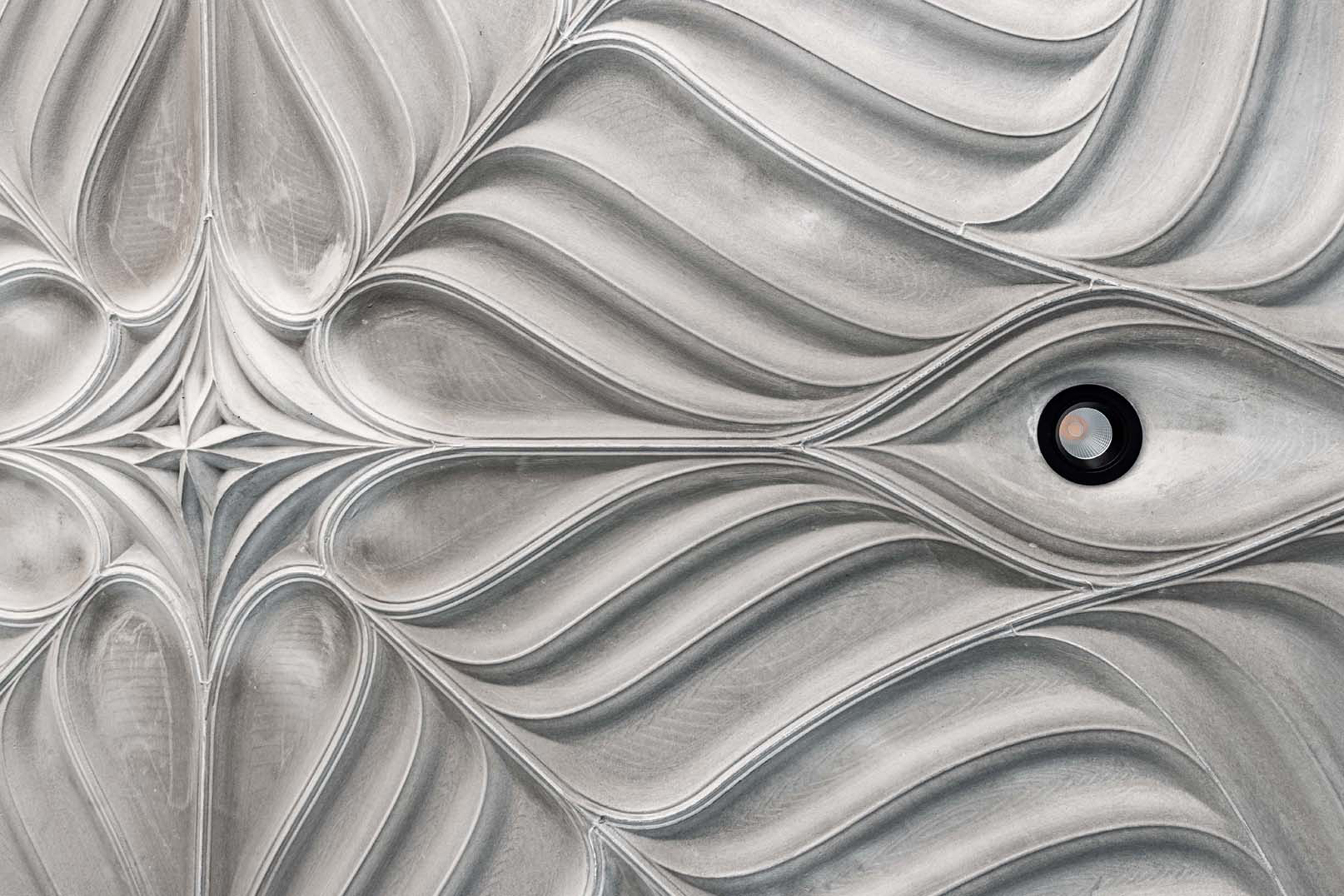
© Andrei Jipa
Nullam dictum felis eu pede mollis pretium. Integer tincidunt. Cras dapibus. Vivamus elementum semper nisi. Aenean vulputate eleifend tellus. Aenean leo ligula, porttitor eu, consequat vitae, eleifend ac, enim. Aliquam lorem ante, dapibus in, viverra quis, feugiat a, tellus. Phasellus viverra nulla ut metus varius laoreet. Quisque rutrum. Aenean imperdiet. Etiam ultricies nisi vel augue. Curabitur ullamcorper ultricies nisi.
The latest example: the HiRes Concrete Slab recently developed by an interdisciplinary team at ETH Zurich for the NEST research building in the Swiss city of Dübendorf, where the thin, slightly vaulted funicular concrete floor was installed in an office space measuring approximately 4 x 5 m at the HiLo research unit of ETH. The scientists presented a precursor to this ribbed slab at the Davos World Economic Forum in 2019. They claim that this construction form represents a material reduction of around 70% compared to a standard flat slab. The trick here is the structurally optimized arrangement of the ribs on the upper side of the ceiling slab, which is approx. 50 mm thick. Moreover, the ceiling in the middle of the space has a rise of around 275 mm. Along the four edges of the room, post-tensioning ties measuring 12 mm in thickness have been integrated into the floor, which means further savings in concrete.
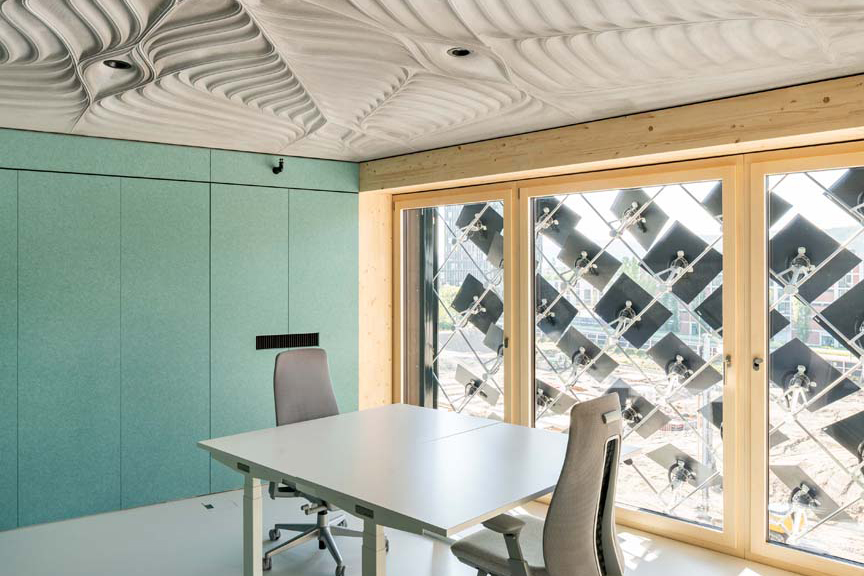
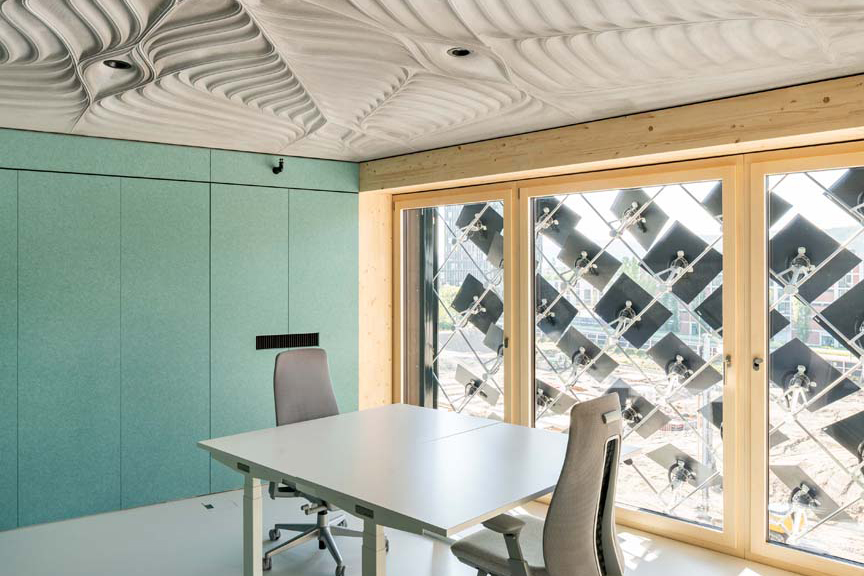
© Roman Keller
The spectacular bottom side of the floor is acoustically optimized. The sound-scattering ridges are most pronounced in the middle of the slab and lie close together; in contrast, towards the walls they diminish to a smooth surface. The slab integrates not only spaces for the lighting system, but also for heating and cooling pipes as well as the barely visible air vents. All the pipes were integrated into the formwork before the concrete was poured.
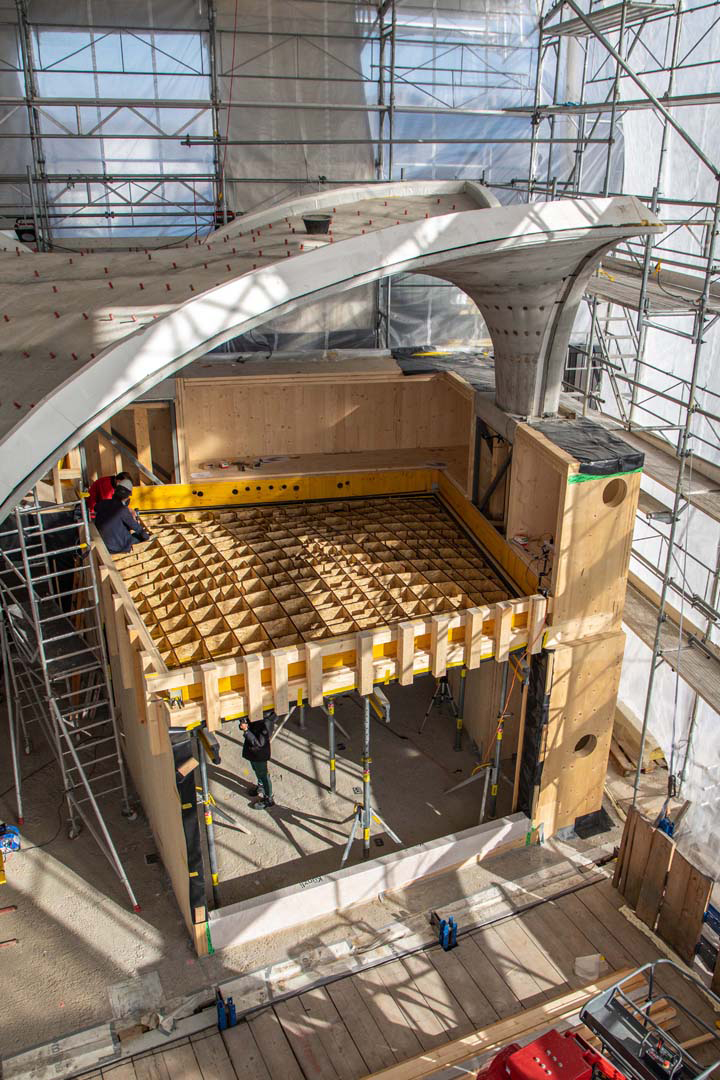
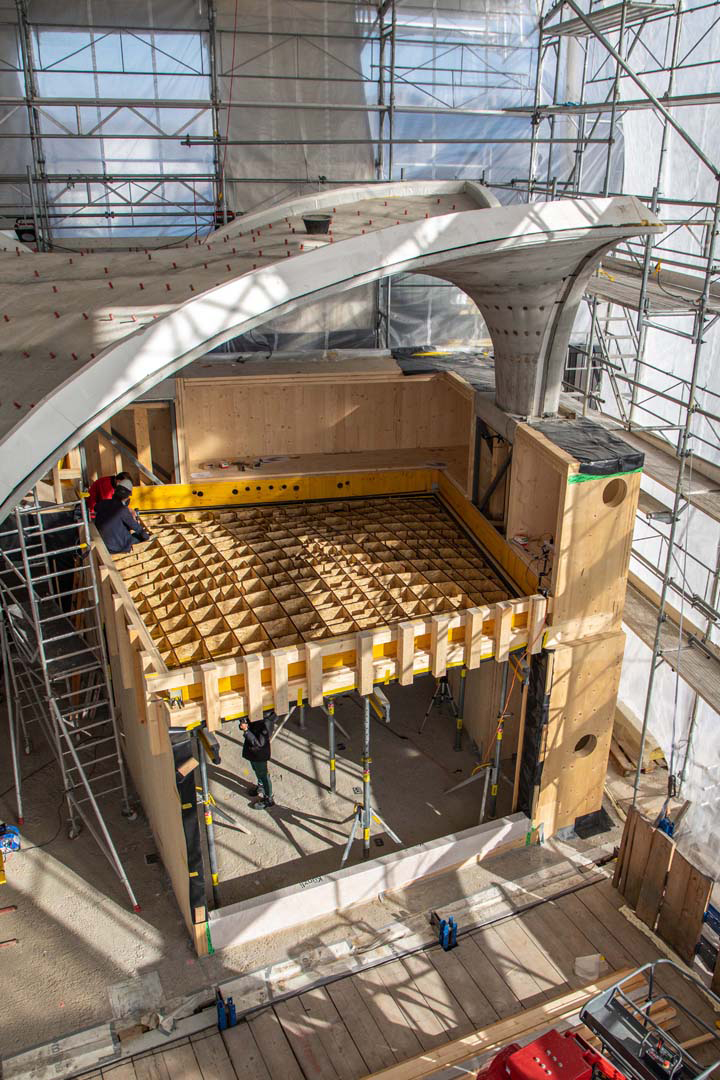
© Lian Stähelin
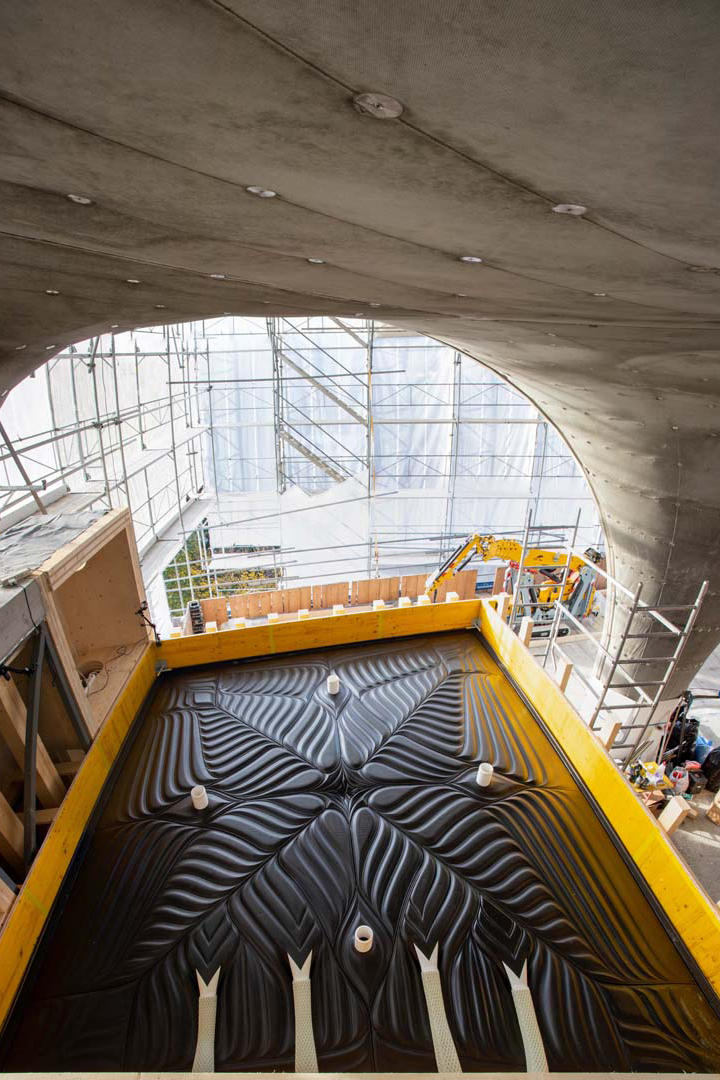
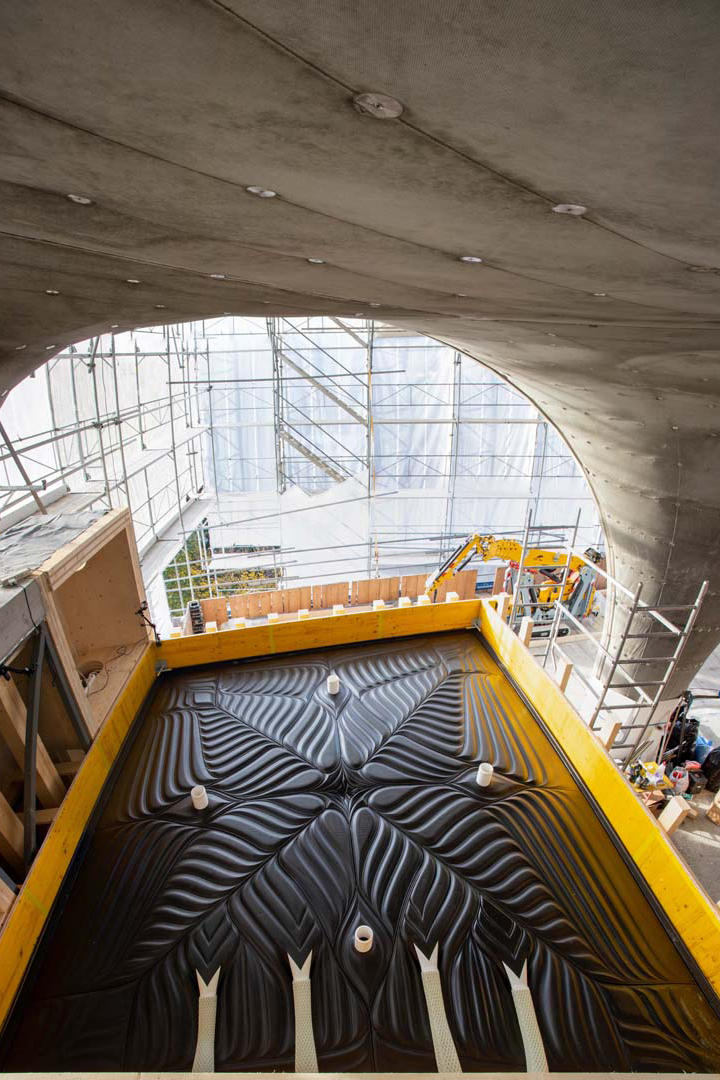
© Andrei Jipa
Digital production processes
The concrete floor was cast in place using 43 3D-printed, small-scale formwork parts for the bottom slab. These were mounted onto a slightly vaulted waffle grid. To make the floor, the ETH team combined three digital production processes: the wood for the waffle grid was laser-cut, and the formwork elements were created using a binder-jet process whereby sand is selectively solidified by the addition of a binding agent. For the small-scale ventilation ducts, the researchers used a technique known as fused deposition modelling (FDM). In FDM, a component is built up in layers of a liquid thermoplastic material which subsequently hardens.
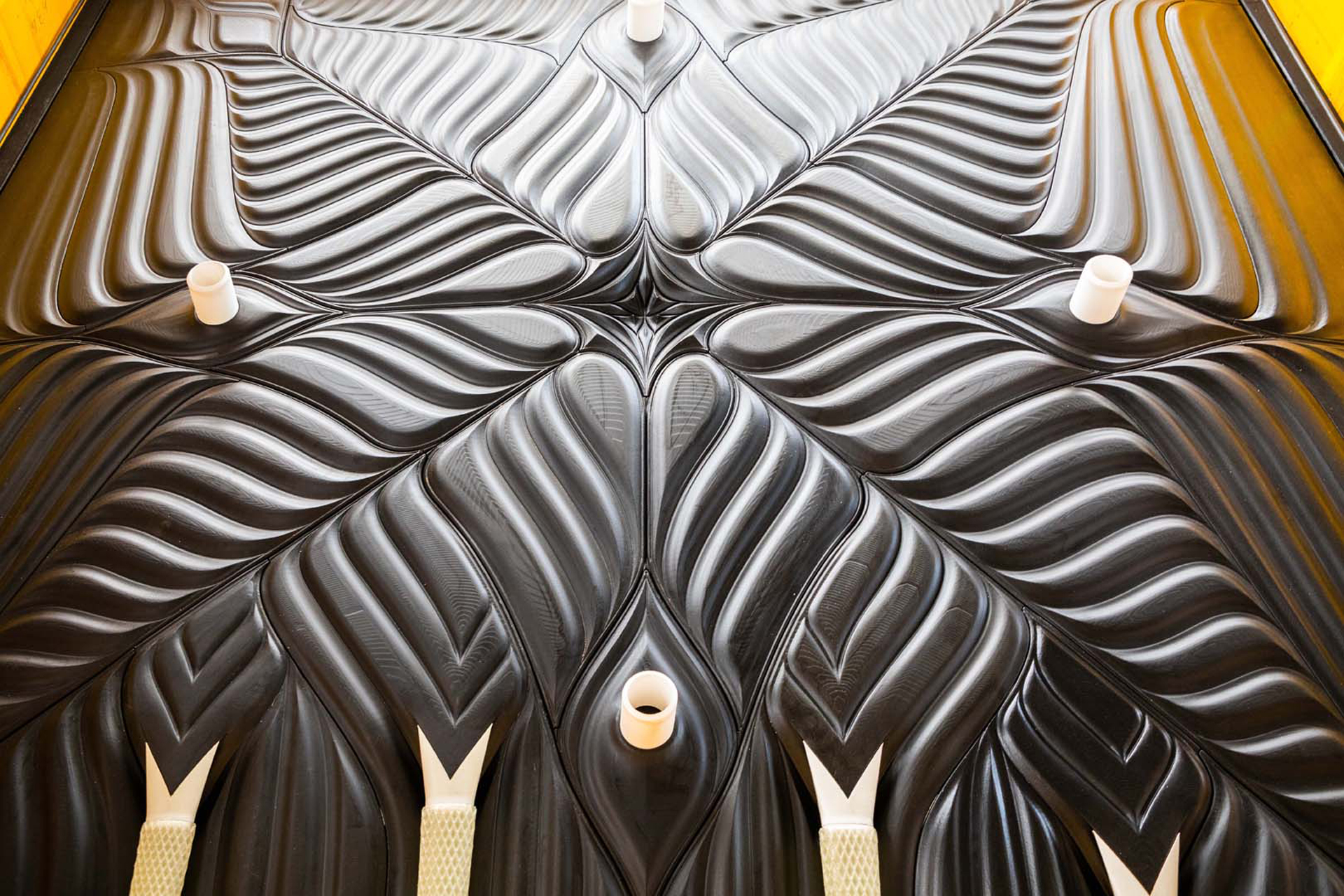
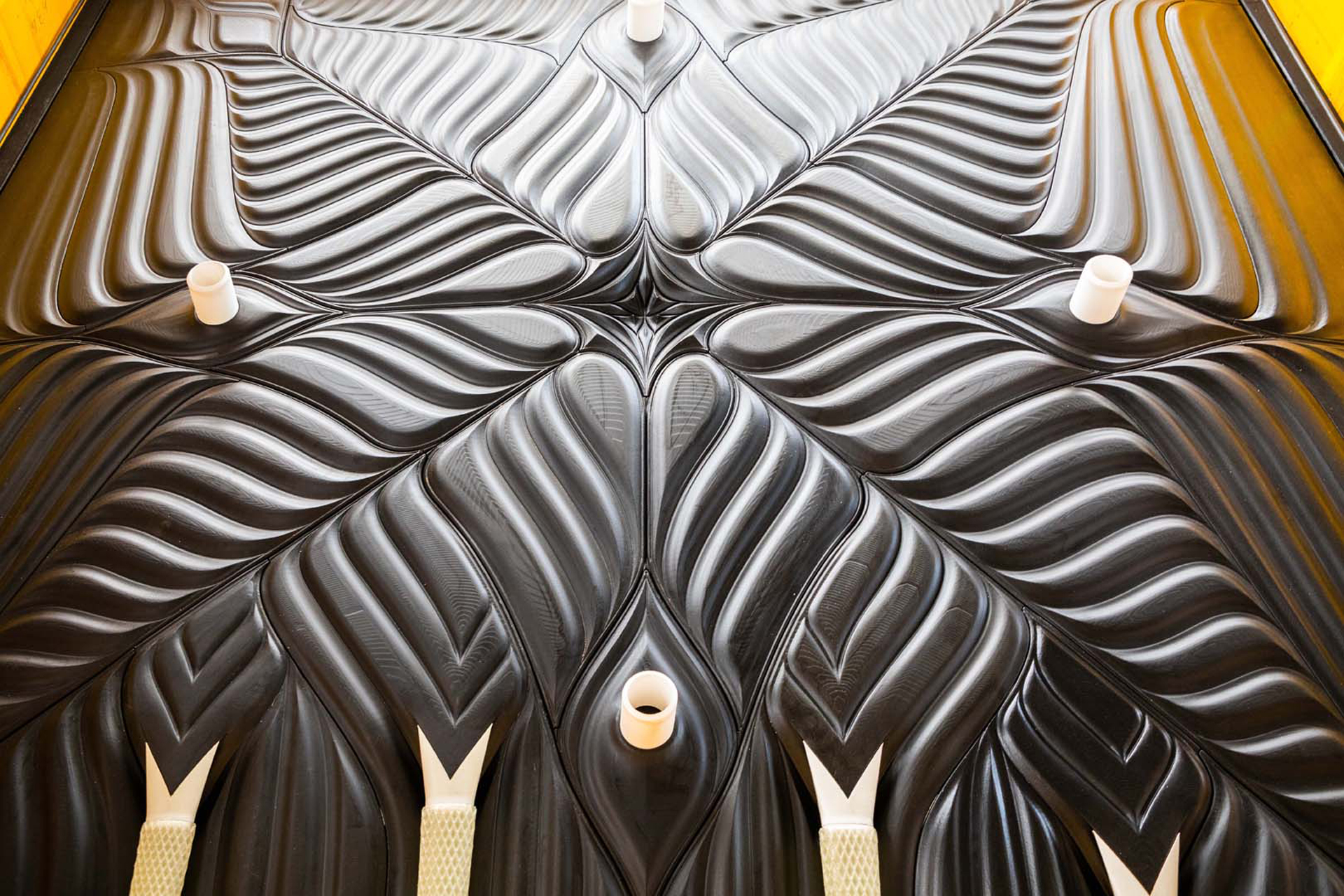
© Andrei Jipa
In comparison, the forming method used for the 50 − 80 mm ribs on the upper side of the slab is considerably simpler. Blocks of CNC wire-cut polyurethane foam serve as the formwork elements; these remain between the ribs as additional insulation after production is complete.
ETH Zürich: DBT (Andrei Jipa, Angela Yoo, Georgia Chousou, Benjamin Dillenburger), BRG (Matthias Rippman, Francesco Ranaudo, Tom Van Mele, Philippe Block), A/S (Gearóid Lydon, Arno Schlueter), ROK Architects (Michael Knauss, Silvan Oesterle)
Partners and sponsors: Empa, NCCR Digital Fabrication, Bürgin Creations, Holcim (Schweiz), BASF (Schweiz), Christenguss