Trocknung formt Holz
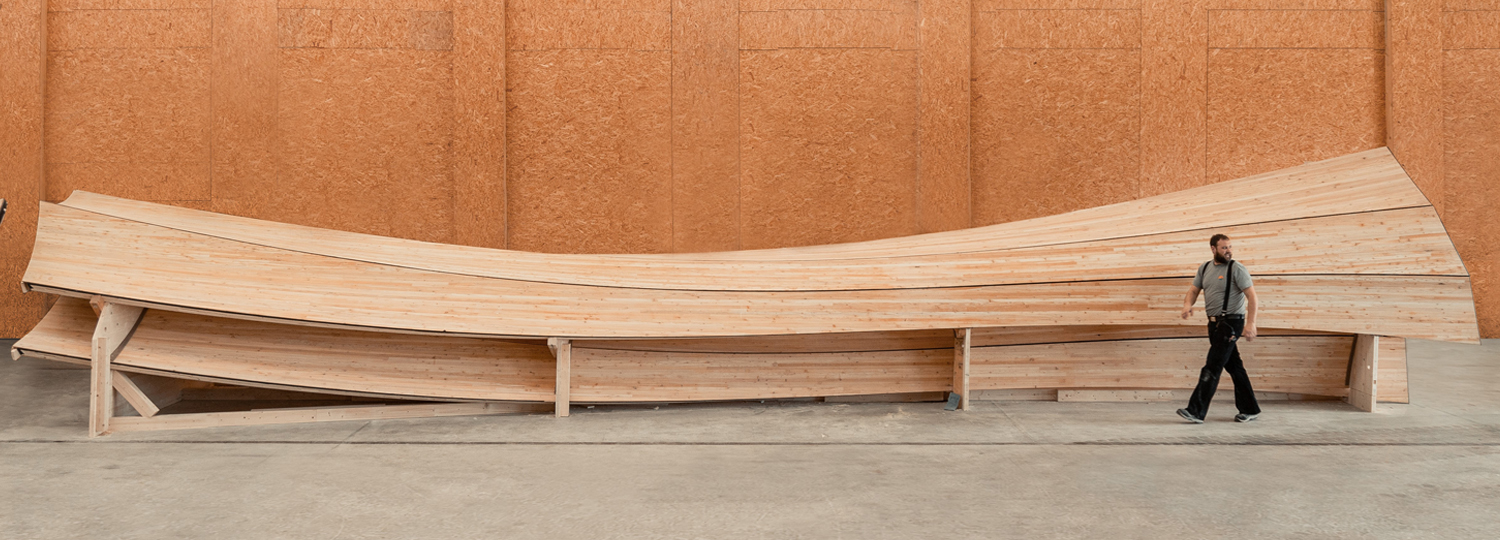
Fertiggestellte Bauteile aus selbstständig gebogenem Lärchenholz vor dem Transport zur Baustelle (Foto: ICD/ITKE University of Stuttgart)
»Programmierung« von Holz
Maßgeblich für die Selbstformung der komplex gekrümmten Bauteile sind der abnehmende Feuchtegehalt und der Schichtaufbau der Bauteile. Im Holzbau verursachen Feuchtigkeitsänderungen normalerweise unerwünschte Verformungen, die möglichst minimiert werden. Dieses feuchtigkeitsbedingte Quellen und Schwinden wird nun genutzt, um die Formänderung aktiv anhand der Berechnungen am digitalen Modell zu steuern.
Holz schrumpft beim Trocknen quer zur Faserrichtung stärker als längs. Werden zwei Schichten Holz zum Bilayer zusammengeklebt, bei dem die Lagen in 0° und 90°-Orientierung der Faserrichtung aufgesetzt sind, verbiegt sich der Bilayer durch das Schrumpfen quer zur Faserrichtung und durch den Widerstand in Faserrichtung. Dieser sich krümmende Bilayer ist das Grundelement des neuen Verfahrens. Durch die Dicke des Elements, seinen Schichtenaufbau, die Jahrringorientierung sowie den variierenden Feuchtigkeitsgehalt des Holzes kann die Krümmung vorab definiert werden. Die Wissenschaftler bezeichnen dies als Materialprogrammierung. So können vordefinierte Krümmungsradien von größeren Bauteilen relativ präzise erreicht werden, wie eine erste baumaßstäbliche Anwendung, der Urbach Turm auf der Remstal Gartenschau 2019, erstmals veranschaulicht.
Fertigung und Fixierung
Die Komponenten werden zunächst als flache Paneele nach computergestützten Modellen hergestellt. Das Fichtenholz, das anfänglich über eine hohe Holzfeuchte verfügt, wird in einem industriell standardisierten Verfahren getrocknet. Die Krümmung ändert sich dabei annähernd proportional zur Abnahme des Feuchtegehalts. Beim Herausnehmen aus der Trocknungskammer – im industrieüblichen Prozess dauert das Trocknen wenige Tage – sind die Elemente entsprechend den Vorgaben gekrümmt. Um die Geometrie zu fixieren, werden sie anschließend auf geformten Lehrgerüsten gelagert und miteinander überlappend laminiert. Es entstehen formstabile Brettsperrholz-Komponenten, die sich im Gegensatz zu konventionellen, im kalt-elastischen Verformungsverfahren herstellten gekrümmten Elementen, durch kaum vorhandene Rückstellkräfte nicht mehr in ihrer Form ändern.
Hochleistungsfähige Konstruktion
Die einfache Anpassung an unterschiedliche Krümmungstypen und -radien eröffnet neue gestalterische Möglichkeiten für dünnwandige, tragende Schalenstrukturen im Holzbau. Die »selbstformende« Fertigung lässt sich in bestehende industrielle Holzverarbeitungs- und Fertigungsabläufe integrieren. Der Prototyp Urbach Turm besteht aus zwölf gekrümmten Bauteilen aus Brettsperrholz. Die Tragkonstruktion hat eine Dicke von 90 mm und weist mit über 14 m Höhe ein Spannweiten-Dicken-Verhältnis von ca. 160:1 auf. Die Krümmung ermöglicht eine schlanke Struktur mit nur 38 kg pro m2 Oberfläche. Die Leichtbauelemente sind durch kreuzweise angeordnete Vollgewindeschrauben verbunden, deren Platzierung und Winkel in Bezug auf ihre statische Ausnutzung optimiert ist. Eine durchgehende Verbindung entlang der Naht sorgt für einen homogenen Lastabtrag.
Die Struktur des Prototyps, der sich an der Schnittstelle von Handwerk, digitaler Innovation und wissenschaftlicher Forschung bewegt, demonstriert die vielseitigen Möglichkeiten der neuartigen gekrümmten Brettsperrholzelemente für eine effiziente, ökologische und ausdrucksstarke Holzarchitektur.
Dieser Beitrag ist auch erschienen in der Fachzeitschrift structure 3/2019.