Schmuckstück im Chaos: »Skylink« am Frankfurter Flughafen
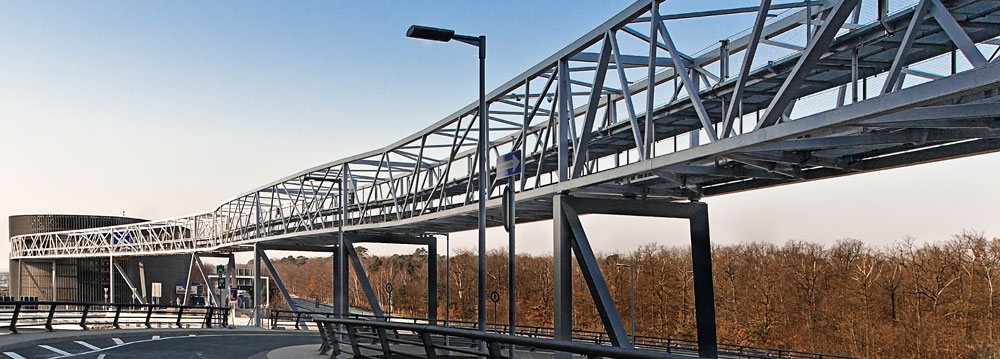
Die erste parametrisch am Computer generierte und optimierte Brücke, die auch gebaut wurde, erhielt eine Auszeichnung beim Preis des Deutschen Stahlbaus 2012. Die zufällig erscheinende Anordnung der Diagonalen ist das Ergebnis eines evolutionären Designprozesses.
Planung: Lengfeld + Wilisch Architekten BDA
Ort: Rhein-Main-Flughafen, D-60547 Frankfurt am Main
Planung: Lengfeld + Wilisch Architekten BDA
Ort: Rhein-Main-Flughafen, D-60547 Frankfurt am Main
Die neue Brücke am Frankfurter Flughafen verbindet das Bürogebäude »The Squaire« mit einem 300 m entfernten Parkhaus und verläuft über eine Reihe von Hauptverkehrsadern und ein Drainagebecken, woraus sich Spannweiten von 12 bis 90 m ergeben. Zwei seilgezogene Kabinenbahnen transportieren Gäste und Passagiere. Die Brücke befindet sich über der Hauptzufahrt zum Terminal 1 am Frankfurter Flughafen. Des Weiteren ist die Brücke von der vorbeiführenden Autobahn und der ICE-Strecke aus zu sehen. Aufgrund dieser exponierten Lage musste die Konstruktion einem sehr hohen ästhetischen Anspruch gerecht werden – die Wahl fiel auf eine Stahlfachwerkbrücke.
Die Fachwerkkonstruktion des Skylink mit seinen Diagonalen stellt eine ingenieurtechnische Besonderheit dar. Die Diagonalen wurden mit einem speziellen Computer-Algorithmus generiert, bei dem die Diagonalen zunächst nach einem Zufallsschema angeordnet werden und danach die gesamte Konstruktion analysiert wird. Die Software ermittelte Bereiche mit höheren Verformungen und Diagonalen ohne Lastübertragung (Nullstäbe) wurden aus der Struktur entfernt bzw. durch die Anwendung eines evolutionären Designprozesses an eine andere, effizientere Position gesetzt. Auf diese Weise ergab sich eine Struktur, die den Anforderungen gerecht wird, aber wie zufällig angeordnet wirkt.
In der Laudatio bei der Preisverleihung am 19. Oktober 2012 hieß es: »Der Skylink ist ein Schmuckstück im städtebaulichen Chaos des Frankfurter Flughafens. Als erste parametrisch am Computer generiert und optimierte Brücke der Welt, die auch realisiert wurde, spannt sich die elegante Stahlkonstruktion in neun geschwungenen Abschnitten über 200 Meter […]. Mit den filigranen Diagonalen, die zufällig platziert scheinen, deren Anordnung in Wahrheit aber dem optimalen Kraftfluss repräsentiert, ist es gelungen die Kabinenfahrt auf dem Skylink zu einem optisch aufregenden Erlebnis zu machen.«
Die Fachwerkkonstruktion des Skylink mit seinen Diagonalen stellt eine ingenieurtechnische Besonderheit dar. Die Diagonalen wurden mit einem speziellen Computer-Algorithmus generiert, bei dem die Diagonalen zunächst nach einem Zufallsschema angeordnet werden und danach die gesamte Konstruktion analysiert wird. Die Software ermittelte Bereiche mit höheren Verformungen und Diagonalen ohne Lastübertragung (Nullstäbe) wurden aus der Struktur entfernt bzw. durch die Anwendung eines evolutionären Designprozesses an eine andere, effizientere Position gesetzt. Auf diese Weise ergab sich eine Struktur, die den Anforderungen gerecht wird, aber wie zufällig angeordnet wirkt.
In der Laudatio bei der Preisverleihung am 19. Oktober 2012 hieß es: »Der Skylink ist ein Schmuckstück im städtebaulichen Chaos des Frankfurter Flughafens. Als erste parametrisch am Computer generiert und optimierte Brücke der Welt, die auch realisiert wurde, spannt sich die elegante Stahlkonstruktion in neun geschwungenen Abschnitten über 200 Meter […]. Mit den filigranen Diagonalen, die zufällig platziert scheinen, deren Anordnung in Wahrheit aber dem optimalen Kraftfluss repräsentiert, ist es gelungen die Kabinenfahrt auf dem Skylink zu einem optisch aufregenden Erlebnis zu machen.«
Geometrie
Die durchgehende Fachwerkkonstruktion besteht aus vier Gurten und hat einen Gesamtquerschnitt von 5 m x 5 m, durch den die Kabinenbahn fährt. In der Mitte, wo sich zwei Kabinen begegnen, beträgt der Querschnitt 5 m x 8 m. An dem Ende der Brücke, wo sie an das Bürogebäude anschließt, kragt sie ungefähr 9 m aus. Über die letzten 2,5 m bildet sich ein gelenkiges Brückenelement aus, das die unterschiedlichen Verformungen zwischen dem Skylink und The Squaire aufnimmt. Durch die horizontale Gleitlagerung (Bewegungsfuge) dieses letzten Brückenelements werden eventuelle Temperaturzwängungen verhindert, die zwischen der Einspannung bei Stütze 3 und dem Bürogebäude auftreten können. Die horizontalen Verformungen in Richtung der Skylinkbrücke am Bürogebäudeende betragen ca. +/- 10 cm.
Die Regelquerschnitte für die Diagonalen sind 120 mm und 140 mm breite, quadratische Hohlkastenprofile mit Wandungsdicken von 10 mm. Für die Ober- und Untergurte wurden ebenfalls quadratische Hohlkasten gewählt, mit Querschnitten von 300 mm x 300 mm und Wandungsdicken von in der Regel 10 mm. Die Diagonalen sind immer so angeordnet, dass die Stege von Gurten und Diagonalen in einer Ebene liegen. Auf diese Weise kollidieren die Diagonalen nicht untereinander und die Biegung der Gurtflansche wird reduziert. Die dadurch entstehende Torsion im Hohlkasten kann durch diesen, bedingt durch seine Bauform, sehr gut abtragen werden. Aufgrund der Ermüdungsbeanspruchung durch den Bahnverkehr wurden Steifen im Anschlusspunkt der Diagonalen in die Gurtprofile eingeschweißt. Die bis zu 17 m hohen Stützen haben einen dreieckigen Querschnitt mit einer Kantenlänge von 635 mm. An den Enden ist die Konstruktion der Skylink-Brücke durch eine Glasfassade geschützt, im Mittelteil hingegen sind die Fachwerkträger nach oben offen und frei sichtbar.
Die durchgehende Fachwerkkonstruktion besteht aus vier Gurten und hat einen Gesamtquerschnitt von 5 m x 5 m, durch den die Kabinenbahn fährt. In der Mitte, wo sich zwei Kabinen begegnen, beträgt der Querschnitt 5 m x 8 m. An dem Ende der Brücke, wo sie an das Bürogebäude anschließt, kragt sie ungefähr 9 m aus. Über die letzten 2,5 m bildet sich ein gelenkiges Brückenelement aus, das die unterschiedlichen Verformungen zwischen dem Skylink und The Squaire aufnimmt. Durch die horizontale Gleitlagerung (Bewegungsfuge) dieses letzten Brückenelements werden eventuelle Temperaturzwängungen verhindert, die zwischen der Einspannung bei Stütze 3 und dem Bürogebäude auftreten können. Die horizontalen Verformungen in Richtung der Skylinkbrücke am Bürogebäudeende betragen ca. +/- 10 cm.
Die Regelquerschnitte für die Diagonalen sind 120 mm und 140 mm breite, quadratische Hohlkastenprofile mit Wandungsdicken von 10 mm. Für die Ober- und Untergurte wurden ebenfalls quadratische Hohlkasten gewählt, mit Querschnitten von 300 mm x 300 mm und Wandungsdicken von in der Regel 10 mm. Die Diagonalen sind immer so angeordnet, dass die Stege von Gurten und Diagonalen in einer Ebene liegen. Auf diese Weise kollidieren die Diagonalen nicht untereinander und die Biegung der Gurtflansche wird reduziert. Die dadurch entstehende Torsion im Hohlkasten kann durch diesen, bedingt durch seine Bauform, sehr gut abtragen werden. Aufgrund der Ermüdungsbeanspruchung durch den Bahnverkehr wurden Steifen im Anschlusspunkt der Diagonalen in die Gurtprofile eingeschweißt. Die bis zu 17 m hohen Stützen haben einen dreieckigen Querschnitt mit einer Kantenlänge von 635 mm. An den Enden ist die Konstruktion der Skylink-Brücke durch eine Glasfassade geschützt, im Mittelteil hingegen sind die Fachwerkträger nach oben offen und frei sichtbar.
Generierungsprozess
Von Anfang an bemühten sich die Architekten, eine unregelmäßige Struktur zu erzeugen, die nicht auf traditionellen strukturellen Typologien beruht. Herkömmliche Top-Down-Methoden eignen sich nicht für ein solches Vorhaben. Daraus ergab sich die Entwicklung eines speziellen Generierungsprozesses unter Verwendung der Computersoftware GENTs, wobei die Struktur nicht vordefiniert sein muss.
Innerhalb definierter Grenzbedingungen werden in kurzer Zeit eine hohe Anzahl an zufälligen Strukturen generiert und berechnet. Für die Berechnung werden die maßgebenden Lastfälle aus der Belastung durch die MiniMetro berücksichtigt. Die generierten Strukturen gehen aus einem iterativen Prozess hervor, bei dem Grundlagen der Evolutionstheorie – wie zum Beispiel Selektion, Mutation und Rekombination – mit herangezogen werden, bis eine möglichst effiziente Struktur gefunden wird. Die Ergebnisse zeigen sehr unregelmäßige Strukturen, Einflüsse aus und auf das Tragverhalten sind komplex und lassen sich nicht auf den ersten Blick ableiten. Die Möglichkeit, existierendes Designvokabular zu erweitern, wurde in Studien belegt. Darüber hinaus können hellere und effektivere Strukturen entwickelt werden, besonders wenn man unregelmäßige Rahmenbedingungen hat.
Parametrisierung
Die Qualität der Lösungen aus generativen Prozessen hängt erheblich von der Größe des Lösungsraumes (die Anzahl der zu optimierenden Parameter) und der Definition der Ziele ab. Um den Lösungsraum effektiv zu reduzieren, muss der Planer eine geeignete Parametrisierung des Problembereiches finden. Im Fall des Skylinks wurde dies über eine angepasste Parametrisierung hinsichtlich der nachfolgenden Ausführung erzielt.
Von Anfang an bemühten sich die Architekten, eine unregelmäßige Struktur zu erzeugen, die nicht auf traditionellen strukturellen Typologien beruht. Herkömmliche Top-Down-Methoden eignen sich nicht für ein solches Vorhaben. Daraus ergab sich die Entwicklung eines speziellen Generierungsprozesses unter Verwendung der Computersoftware GENTs, wobei die Struktur nicht vordefiniert sein muss.
Innerhalb definierter Grenzbedingungen werden in kurzer Zeit eine hohe Anzahl an zufälligen Strukturen generiert und berechnet. Für die Berechnung werden die maßgebenden Lastfälle aus der Belastung durch die MiniMetro berücksichtigt. Die generierten Strukturen gehen aus einem iterativen Prozess hervor, bei dem Grundlagen der Evolutionstheorie – wie zum Beispiel Selektion, Mutation und Rekombination – mit herangezogen werden, bis eine möglichst effiziente Struktur gefunden wird. Die Ergebnisse zeigen sehr unregelmäßige Strukturen, Einflüsse aus und auf das Tragverhalten sind komplex und lassen sich nicht auf den ersten Blick ableiten. Die Möglichkeit, existierendes Designvokabular zu erweitern, wurde in Studien belegt. Darüber hinaus können hellere und effektivere Strukturen entwickelt werden, besonders wenn man unregelmäßige Rahmenbedingungen hat.
Parametrisierung
Die Qualität der Lösungen aus generativen Prozessen hängt erheblich von der Größe des Lösungsraumes (die Anzahl der zu optimierenden Parameter) und der Definition der Ziele ab. Um den Lösungsraum effektiv zu reduzieren, muss der Planer eine geeignete Parametrisierung des Problembereiches finden. Im Fall des Skylinks wurde dies über eine angepasste Parametrisierung hinsichtlich der nachfolgenden Ausführung erzielt.
Vordefiniert waren je zwei Ober- und Untergurte, die durch diagonale Elemente miteinander verbunden werden. Die Diagonalen ermöglichen den Lasttransfer der Brücke. Je drei Diagonalen werden miteinander verbunden und formen so eine Verbindungseinheit, eine sogenannte »Klammer«. Jede Klammer besteht aus einer horizontalen Diagonale, die das »Dach« bzw. den »Boden« der Brücke bilden, sowie zwei vertikalen Diagonalen, die in den seitlichen Aussteifungsebenen der Brücke angeordnet sind.
Auf diese Weise bildet jede Klammer ein »U« über die Ober- bzw. Untergurte. Um die Montage der Struktur zu vereinfachen, wurden die Klammern in zwei Gruppen geordnet. Des Weiteren liegen sie in zwei Ebenen, die um die Breite der Diagonalen voneinander versetzt sind. Die Diagonalen sind durch Knotenpunkte an den Gurten gekennzeichnet.
Die Parametrisierung ist so definiert, dass jeder Knoten seinem Nachbarknoten entspricht. Dadurch kreuzen sich Elemente aus derselben Gruppe nicht. Kreuzungspunkte entstehen lediglich zwischen Elementen aus den zwei verschiedenen Gruppen. Durch die Parametrisierung lassen sich nicht nur komplizierte Knotenpunkte vermeiden, auch der Lösungsraum wird erheblich verringert.
Zielsetzung
Eigengewicht und die maximale Durchbiegung sind die Anhaltspunkte für die effektive Abschätzung des Tragverhaltens der Struktur. Während die Durchbiegung einen bestimmten Grenzwert nicht überschreiten darf, sollte das Gewicht so weit wie möglich reduziert werden. Der Grenzwert der maximalen Durchbiegung wurde nach nur wenigen Generierungen erzielt. Somit verblieb das Augenmerk auf der Reduzierung des Gewichts. Um eine realistische Einschätzung zu gewährleisten, wurden die einzelnen Elemente entsprechend ihrer spezifischen Spannungsausnutzung bemessen.
Die Dimensionierung ist eine Methode, Fachwerkstrukturen zu optimieren. Dadurch bleibt die Geometrie unverändert, nur die Profile der einzelnen Elemente werden den jeweiligen Lasten und Spannungen angepasst. Um die Einflüsse auf die jeweiligen Elemente zu ermitteln, sind die maßgebenden Spannungen aus allen Belastungen zu berechnen. Auf dieser Grundlage vergrößern oder verkleinern sich die Profile der Fachwerkstäbe. Bei jeder dieser Optimierungen verändert sich das Gesamtsystem, Kräfte werden anders verteilt und der Einfluss auf jeden einzelnen Stab ändert sich. Demzufolge wird dieser Optimierungsprozess solange wiederholt, bis sich kein Stab mehr ändert.
Auf diese Weise bildet jede Klammer ein »U« über die Ober- bzw. Untergurte. Um die Montage der Struktur zu vereinfachen, wurden die Klammern in zwei Gruppen geordnet. Des Weiteren liegen sie in zwei Ebenen, die um die Breite der Diagonalen voneinander versetzt sind. Die Diagonalen sind durch Knotenpunkte an den Gurten gekennzeichnet.
Die Parametrisierung ist so definiert, dass jeder Knoten seinem Nachbarknoten entspricht. Dadurch kreuzen sich Elemente aus derselben Gruppe nicht. Kreuzungspunkte entstehen lediglich zwischen Elementen aus den zwei verschiedenen Gruppen. Durch die Parametrisierung lassen sich nicht nur komplizierte Knotenpunkte vermeiden, auch der Lösungsraum wird erheblich verringert.
Zielsetzung
Eigengewicht und die maximale Durchbiegung sind die Anhaltspunkte für die effektive Abschätzung des Tragverhaltens der Struktur. Während die Durchbiegung einen bestimmten Grenzwert nicht überschreiten darf, sollte das Gewicht so weit wie möglich reduziert werden. Der Grenzwert der maximalen Durchbiegung wurde nach nur wenigen Generierungen erzielt. Somit verblieb das Augenmerk auf der Reduzierung des Gewichts. Um eine realistische Einschätzung zu gewährleisten, wurden die einzelnen Elemente entsprechend ihrer spezifischen Spannungsausnutzung bemessen.
Die Dimensionierung ist eine Methode, Fachwerkstrukturen zu optimieren. Dadurch bleibt die Geometrie unverändert, nur die Profile der einzelnen Elemente werden den jeweiligen Lasten und Spannungen angepasst. Um die Einflüsse auf die jeweiligen Elemente zu ermitteln, sind die maßgebenden Spannungen aus allen Belastungen zu berechnen. Auf dieser Grundlage vergrößern oder verkleinern sich die Profile der Fachwerkstäbe. Bei jeder dieser Optimierungen verändert sich das Gesamtsystem, Kräfte werden anders verteilt und der Einfluss auf jeden einzelnen Stab ändert sich. Demzufolge wird dieser Optimierungsprozess solange wiederholt, bis sich kein Stab mehr ändert.
Ermüdungsbelastung
Aufgrund der großen Bauhöhe von 5 m erhielt die Brücke ein sehr geringes Eigengewicht, was die Konstruktion sehr anfällig für Ermüdungslasten macht. In den Hohlkastenprofilen der Gurte wurden Steifen angeordnet, um diese Lasten aus den Diagonalen aufzunehmen. Die Ermüdungsbemessungen wurden auf der Grundlage des konstruktiven »Hot-spot-Spannungsansatzes« nach der IIW Richtlinie »Fatigue design of welded joints and components« (dt.: Ermüdungsbemessungen für geschweißte Verbindungen und Bauteile) durchgeführt, da eine klare Zuordnung zu bekannten Kerbfällen nicht möglich war. Die Knotenpunkte wurden mit der Finite-Elemente-Software RFEM modelliert.
Nach der oben genannten Methode werden die an einem finiten Schalenelement-Modell ermittelten Spannungen mit den zulässigen Spannungen für verschiedene Schweißtypen verglichen. Um Spannungsspitzen, die im Modell aufgrund der singulären Verbindung der einzelnen Schalenelemente auftreten, auszuschließen, wird eine reduzierte Spannung am »hot spot« ermittelt, wo Schweißnaht und Material miteinander verbunden werden und ein möglicher Versagenspunkt entsteht. Diese reduzierte Spannung wird dann mit den zulässigen Spannungen verglichen. Im vorliegenden Fall des Skylinks wurden Spannungen von 90 N/mm² für 2 Millionen Lastzyklen und 78 N/mm² für 3,05 Millionen Lastzyklen angenommen – letztere spiegeln eine Nutzung der Brücke von 50 Jahren wider.
Fertigung und Montage
Für die gesamte Stahlstruktur, d. h. die Brückenkonstruktion inklusive der acht Stützen, wurden über 500 t Stahl verbaut. Bei der Vormontage in der Werkstatt wurden sowohl die vier Gurte inklusive aller Steifen zusammengeschweißt als auch die dreiecksförmigen Stützen. Des Weiteren wurden alle anderen Profile auf die korrekte Länge zugeschnitten. Die Außenseite der Gurte erhielt eine Markierung für die Lage der Steifen, damit die Diagonalen an der richtigen Stelle angeschlossen werden.
Aufgrund der großen Abmessungen war es unmöglich, Teile der Brücke bereits vorgefertigt auf die Baustelle zu transportieren. Alle Einzelteile wurden lose angeliefert und vor Ort zusammengebaut. Auf der Baustelle wurde die Brücke in acht Elemente aufgeteilt, die zwischen den Momentennullpunkten spannen. Die Arbeiter montierten die Elemente am Boden vor und jeweils zwei Großkräne hoben sie ein. Dies erfolgte teilweise in der Nacht, da unter anderem auch die Zufahrt zum Flughafen für den Einhub gesperrt werden musste. Im Anschluss wurden die Elemente zusammengeschweißt und die Endbeschichtung aufgetragen. Dabei hing das jeweils neueste Element noch am Kran. Die Fertigung erfolgte praktisch am Baufeld. Die größten Brückensegmente erreichten ein Gewicht von über 110 Tonnen und eine Länge von bis zu 90 Metern.
Aufgrund der großen Bauhöhe von 5 m erhielt die Brücke ein sehr geringes Eigengewicht, was die Konstruktion sehr anfällig für Ermüdungslasten macht. In den Hohlkastenprofilen der Gurte wurden Steifen angeordnet, um diese Lasten aus den Diagonalen aufzunehmen. Die Ermüdungsbemessungen wurden auf der Grundlage des konstruktiven »Hot-spot-Spannungsansatzes« nach der IIW Richtlinie »Fatigue design of welded joints and components« (dt.: Ermüdungsbemessungen für geschweißte Verbindungen und Bauteile) durchgeführt, da eine klare Zuordnung zu bekannten Kerbfällen nicht möglich war. Die Knotenpunkte wurden mit der Finite-Elemente-Software RFEM modelliert.
Nach der oben genannten Methode werden die an einem finiten Schalenelement-Modell ermittelten Spannungen mit den zulässigen Spannungen für verschiedene Schweißtypen verglichen. Um Spannungsspitzen, die im Modell aufgrund der singulären Verbindung der einzelnen Schalenelemente auftreten, auszuschließen, wird eine reduzierte Spannung am »hot spot« ermittelt, wo Schweißnaht und Material miteinander verbunden werden und ein möglicher Versagenspunkt entsteht. Diese reduzierte Spannung wird dann mit den zulässigen Spannungen verglichen. Im vorliegenden Fall des Skylinks wurden Spannungen von 90 N/mm² für 2 Millionen Lastzyklen und 78 N/mm² für 3,05 Millionen Lastzyklen angenommen – letztere spiegeln eine Nutzung der Brücke von 50 Jahren wider.
Fertigung und Montage
Für die gesamte Stahlstruktur, d. h. die Brückenkonstruktion inklusive der acht Stützen, wurden über 500 t Stahl verbaut. Bei der Vormontage in der Werkstatt wurden sowohl die vier Gurte inklusive aller Steifen zusammengeschweißt als auch die dreiecksförmigen Stützen. Des Weiteren wurden alle anderen Profile auf die korrekte Länge zugeschnitten. Die Außenseite der Gurte erhielt eine Markierung für die Lage der Steifen, damit die Diagonalen an der richtigen Stelle angeschlossen werden.
Aufgrund der großen Abmessungen war es unmöglich, Teile der Brücke bereits vorgefertigt auf die Baustelle zu transportieren. Alle Einzelteile wurden lose angeliefert und vor Ort zusammengebaut. Auf der Baustelle wurde die Brücke in acht Elemente aufgeteilt, die zwischen den Momentennullpunkten spannen. Die Arbeiter montierten die Elemente am Boden vor und jeweils zwei Großkräne hoben sie ein. Dies erfolgte teilweise in der Nacht, da unter anderem auch die Zufahrt zum Flughafen für den Einhub gesperrt werden musste. Im Anschluss wurden die Elemente zusammengeschweißt und die Endbeschichtung aufgetragen. Dabei hing das jeweils neueste Element noch am Kran. Die Fertigung erfolgte praktisch am Baufeld. Die größten Brückensegmente erreichten ein Gewicht von über 110 Tonnen und eine Länge von bis zu 90 Metern.
Stahlbau
Wie die meisten filigran erscheinenden Konstruktionen mit »tragender Rolle« stellten auch die Stäbe im Skylink eine große Herausforderung für den Stahlbauer dar. Die Stahlknoten zwischen den Ober- und Untergurten und den Verbindungen waren sehr komplex.
Einerseits bestand die Herausforderung in der Art der Struktur selbst. Es handelt sich dabei um eine unregelmäßige Fachwerkkonstruktion aus Hohlprofilen mit unterschiedlichen Stäben. Zudem gab es in der tragenden Struktur keine Schraubverbindungen, d. h. es wurden alle Stäbe mittels Schweißnähten verbunden. Dies stellte sowohl an den Zusammenbau als auch an die Schweißermannschaft sehr hohe Anforderungen. Insgesamt wurden ca. 1000 Verbindungsstäbe in der Brücke verbaut, die rund 300 Meter lang ist und in 16 bis 18 Metern Höhe verläuft.
Projektdaten Architektur: Lengfeld & Willisch Architekten, Darmstadt
Tragwerk: B+G Ingenieure Bollinger und Grohmann GmbH, Frankfurt am Main
Stahlbau: Stahlbau Pichler GmbH, Bozen
Bauherr: IVG THE SQUAIRE Parking GmbH & Co. KG, Frankfurt am Main
Minimetro: Leitner AG, Sterzing
Bericht über alle Gewinner beim Preis des Deutschen Stahlbaues 2012
Wie die meisten filigran erscheinenden Konstruktionen mit »tragender Rolle« stellten auch die Stäbe im Skylink eine große Herausforderung für den Stahlbauer dar. Die Stahlknoten zwischen den Ober- und Untergurten und den Verbindungen waren sehr komplex.
Einerseits bestand die Herausforderung in der Art der Struktur selbst. Es handelt sich dabei um eine unregelmäßige Fachwerkkonstruktion aus Hohlprofilen mit unterschiedlichen Stäben. Zudem gab es in der tragenden Struktur keine Schraubverbindungen, d. h. es wurden alle Stäbe mittels Schweißnähten verbunden. Dies stellte sowohl an den Zusammenbau als auch an die Schweißermannschaft sehr hohe Anforderungen. Insgesamt wurden ca. 1000 Verbindungsstäbe in der Brücke verbaut, die rund 300 Meter lang ist und in 16 bis 18 Metern Höhe verläuft.
Projektdaten Architektur: Lengfeld & Willisch Architekten, Darmstadt
Tragwerk: B+G Ingenieure Bollinger und Grohmann GmbH, Frankfurt am Main
Stahlbau: Stahlbau Pichler GmbH, Bozen
Bauherr: IVG THE SQUAIRE Parking GmbH & Co. KG, Frankfurt am Main
Minimetro: Leitner AG, Sterzing
Bericht über alle Gewinner beim Preis des Deutschen Stahlbaues 2012